Discover the Advantages of In-House Metal Fabrication for Quality and Timely Delivery
By:Admin
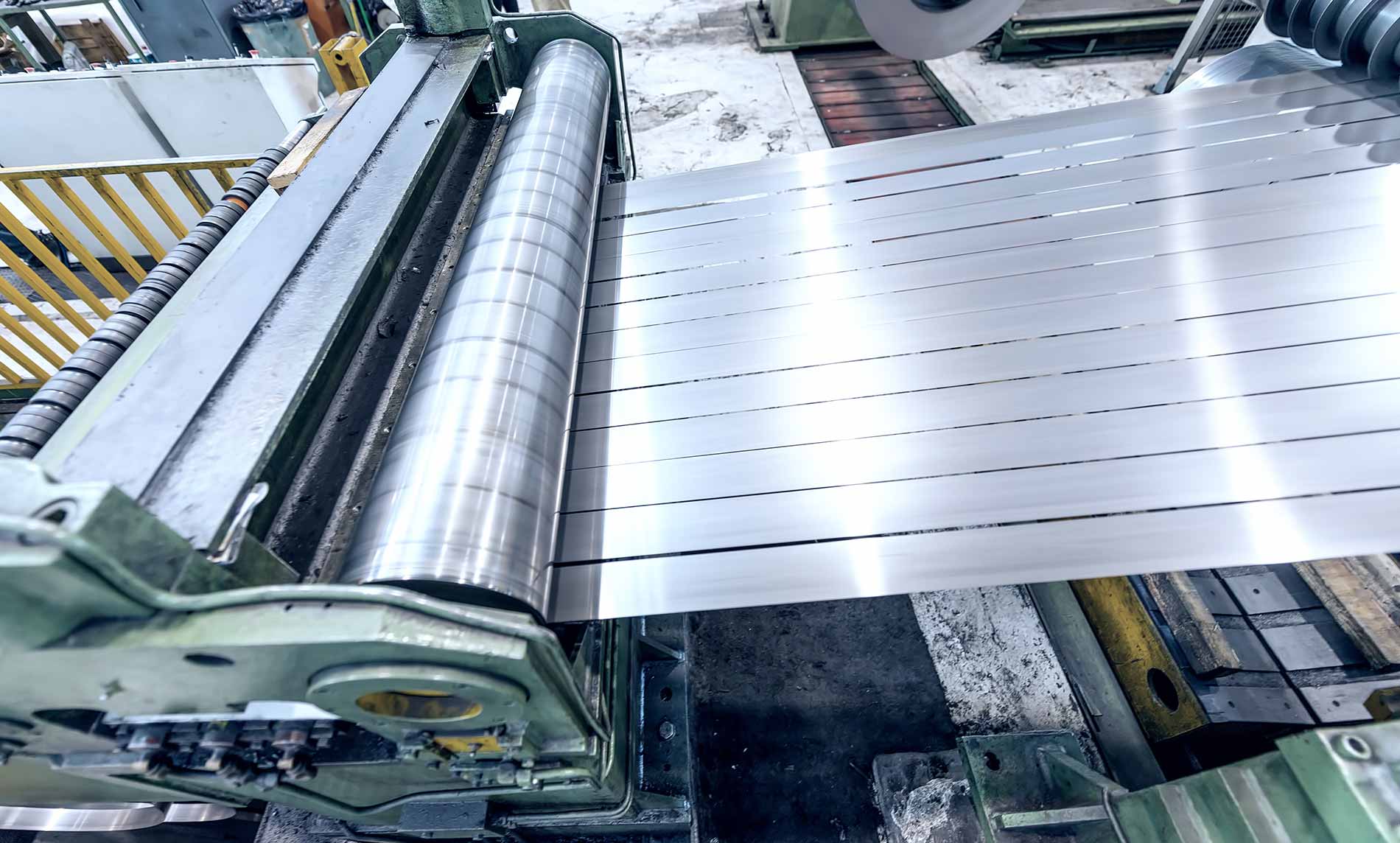
Sheet metal fabrication has come a long way since its inception. It has become an indispensable part of various industries and is used extensively for a multitude of purposes. Be it aerospace, automotive, construction, or any other industry – sheet metal fabrication is crucial in all of them.
Although there are numerous methods of sheet metal fabrication, sheet metal panel fabrication has gained immense popularity among manufacturers. The primary reason for its popularity is the accuracy and precision it offers while fabricating metal panels.
Let's delve deeper into the aspects of sheet metal panel fabrication and understand how it can help manufacturers in their metal fabrication needs.
What is Sheet Metal Panel Fabrication?
Sheet metal panel fabrication is a process that involves cutting, folding, and shaping sheet metal into panels. These panels can be of various shapes and sizes, and the fabrication process can be customized as per the requirement.
Sheet metal panel fabrication involves using various tools such as laser cutting machines, CNC punching machines, and hydraulic press brakes. These machines are highly efficient and can provide accurate and precise output with utmost consistency.
Advantages of Sheet Metal Panel Fabrication
1. Precision – As stated earlier, sheet metal panel fabrication provides a high degree of precision and accuracy. The cutting and folding are done with utmost care and attention to detail, ensuring that the metal panels meet the required specifications.
2. Customization – Sheet metal panel fabrication can be customized to cater to the specific needs of the manufacturer. This versatility allows manufacturers to produce metal panels of various shapes, sizes, and thicknesses. This flexibility is not present in other methods of metal fabrication.
3. Efficiency – Sheet metal panel fabrication is highly efficient and can deliver output at a much quicker rate than other methods of metal fabrication. The use of advanced machines enhances the efficiency of the process, making it an ideal choice for manufacturers who want to increase their production speed.
4. Cost-Effective – Sheet metal panel fabrication can be cost-effective in the long run. The high degree of precision and accuracy results in minimal wastage of material, making it a cost-effective method for manufacturers who want to cut down on their raw material costs.
Conclusion
Sheet metal panel fabrication has become an integral part of various industries. It offers precision, customization, efficiency, and cost-effectiveness, making it the ultimate solution for all metal fabrication needs. If you want to streamline your metal fabrication process and improve your production speed, sheet metal panel fabrication is an ideal choice.
So, if you are looking for a reliable metal fabrication service provider, look no further than sheet metal panel fabrication experts. They can help you with all your metal fabrication needs, ensuring that the end product meets your specifications.
Company News & Blog
Sheet Metal: A Fundamental Form in Metalworking
Title: Sheet Metal Flat: Revolutionizing Industrial Fabrication ProcessesIntroduction:(sheet metal flat logo)Sheet Metal Flat is a renowned leader in the field of sheet metal fabrication. With a commitment to innovation and quality, the company continues to revolutionize the manufacturing industry. Their expertise lies in the production of thin, flat pieces of metal that can be easily cut and shaped into various forms. This article delves into the significance of sheet metal fabrication, explores the various applications, and highlights Sheet Metal Flat's contributions to this field.Importance of Sheet Metal Fabrication:Sheet metal fabrication plays a pivotal role in numerous industries, making it one of the fundamental forms used in metalworking. By utilizing industrial processes, sheet metal is transformed into thin, flat pieces which can then be molded into a variety of shapes. This versatility enables the creation of countless everyday objects that are an integral part of our lives.Applications of Sheet Metal:The applications of sheet metal fabrication are vast and diverse. From the automotive sector to construction, aerospace, and even household appliances, sheet metal is an essential component in the production of various products. It is widely used in the manufacturing of automobile parts, including body panels, chassis, and engine components due to its durability, strength, and resistance to corrosion.In the construction industry, sheet metal is utilized for roofing, facades, and structural elements due to its lightweight nature and high durability. The aerospace industry leverages sheet metal for aircraft structures, providing strength, stability, and resilience at high altitudes. In household appliances, sheet metal is employed in the manufacturing of refrigerators, stoves, and washing machines due to its ability to withstand high temperatures and repeated use.Sheet Metal Flat: Pioneers in Fabrication:Sheet Metal Flat has emerged as a reliable and innovative player in the sheet metal fabrication industry. The company's commitment to cutting-edge technology and exceptional quality has positioned them as a distinguished leader.Efficient Manufacturing Processes: Sheet Metal Flat employs state-of-the-art machinery and equipment to ensure precision and efficiency in their manufacturing processes. From laser cutting to stamping, bending, and welding, they have perfected every stage of fabrication. This enables them to deliver superior end products while ensuring timely production.Custom Solutions: Recognizing the unique requirements of each client, Sheet Metal Flat offers customized solutions tailored to suit their specific needs. Their team of experienced technicians works closely with customers, providing expert guidance and utilizing cutting-edge software to design and create flawless sheet metal components.Quality Assurance: Sheet Metal Flat is committed to delivering products of the highest quality. Rigorous quality control measures, including inspections at different stages of production, are in place to ensure that every piece meets the highest standards. By adhering to strict quality control protocols, Sheet Metal Flat has fostered long-lasting relationships with their clients.Environmental Responsibility: In an era of increasing environmental awareness, Sheet Metal Flat is committed to minimizing their carbon footprint. They have implemented eco-friendly practices such as recycling scrap metal, reducing waste generation, and incorporating energy-efficient machinery. By choosing Sheet Metal Flat, customers can align with their sustainability goals.Conclusion:Sheet Metal Flat's contribution to the sheet metal fabrication industry cannot be understated. With their innovative manufacturing processes, commitment to quality, and dedication to customer satisfaction, they have set new benchmarks in the field. As the demand for sheet metal continues to grow across various sectors, Sheet Metal Flat is poised to remain at the forefront, constantly pushing the boundaries of possibility and redefining the standards for industrial metalworking.
Digitally Controlled Solutions for Precise Metal Bending in Steel, Stainless Steel, and Aluminum
: How Digitally Controlled Solutions Are Revolutionizing TFE Bending ServicesSheet metal bending has been an essential part of manufacturing since the industrial revolution, but advancements in digital control have allowed for greater levels of precision and efficiency. At TFE, these cutting-edge techniques are being applied to create bespoke sheet metal bending parts of the highest quality and accuracy.In 2018, TFE invested in new bending machines with digital control capabilities, allowing them to meet the increasing requirements of their clients. These machines provide the ability to bend a range of materials including steel, stainless steel, and aluminum, and the accuracy of the multi-station bending press allows for the creation of complex geometries with ease.The use of digital control allows TFE to achieve unparalleled precision, making it possible to create parts with crushed bends or plunging without the need for further reworking. This technology also ensures exceptional repeatability, allowing for a faster turnaround time on orders.The TFE bent metal parts portfolio is comprehensive, covering angular bending, variable radius bending, and crushed bends. However, TFE's capabilities don't stop there. They have also developed innovative methods for large radius stretching, an alternative to rolling or in addition to it. This approach provides unique opportunities for niche applications that require specific shapes of sheet metal parts.TFE takes great pride in their commitment to quality, and their innovative techniques guarantee a constant level of excellence. The company's digitally controlled bending methods allow for excellent man-machine complementarity, resulting in the highest levels of efficiency and productivity.In conclusion, TFE's bending services have been transformed with the integration of digitally controlled bending machines. These advanced techniques allow for the creation of bespoke parts with exceptional levels of accuracy, repeatability, and quality. If you're in the market for sheet metal bending parts, look no further than TFE for the most innovative and precise solutions. Keywords: TFE Bending, Sheet Metal Bending Parts, Digital Control, Bending Machines, Multi-Station Bending Press, Repeatability, Angular Bending, Variable Radius Bending, Crushed Bends, Large Radius Stretching, Man-Machine Complementarity, Precision, Efficiency, Productivity.
High-Quality Fuschia Waterborne 0.60mm PU Synthetic Leather with Suede Fabric Backing
In recent years, the demand for synthetic leather has increased rapidly worldwide. Synthetic leather has become a popular material choice for a variety of industries such as fashion, automotive, furniture, and sports equipment, among others. This is because synthetic leather offers many benefits such as durability, versatility, and cost-effectiveness. In China, one of the leading synthetic leather manufacturers is (brand name removed).One of their most innovative synthetic leather products is their Waterborne 0.60mm PU Synthetic Leather with Suede Fabric Backing in Fuschia Color. This particular product is made of high-quality material and has a sleek and smooth finish which makes it perfect for use in products like high-end fashion items, bags, and accessories. This synthetic leather has a suede fabric backing which provides the added benefit of breathability and comfort. This feature makes it a suitable option for footwear, soles, and insoles.China has become a hub for synthetic leather manufacturing, and (brand name removed) leads the way in developing innovative and high-quality synthetic leather products. They use advanced technology and equipment to produce synthetic leather that meets the highest standards of quality and performance. As a result, they have become one of the most sought-after synthetic leather suppliers in China, and their products are exported to various countries around the world.The Waterborne 0.60mm PU Synthetic Leather with Suede Fabric Backing in Fuschia Color is not only a quality product, but it is also offered at an affordable synthetic leather price. (brand name removed) provides their clients with competitive synthetic leather prices while maintaining the highest quality standards for their products. This has led to increased demand for their products from both local and international markets.Apart from providing quality products at affordable synthetic leather prices, (brand name removed) is also committed to environmental protection. They use water-based technology during the production of their synthetic leather products, which significantly reduces the amount of harmful chemicals released into the environment. The water-based technology also produces less waste material, which reduces waste disposal costs and carbon footprint.In conclusion, the demand for synthetic leather is growing rapidly, and China is at the forefront of synthetic leather manufacturing. (brand name removed) is a leading supplier of synthetic leather in China, and their Waterborne 0.60mm PU Synthetic Leather with Suede Fabric Backing in Fuschia Color is a high-quality product that is popular in various industries. Their commitment to using environmentally friendly technology and providing affordable synthetic leather prices has made them a preferred choice among their clients. For those looking to purchase high-quality synthetic leather products, (brand name removed) is a reliable and trusted supplier.
Fast and Accurate CNC Turning Services for Precision Parts
Lathe machines are essential tools in the world of manufacturing. They are responsible for the creation of many of the intricate components that make up various products. Among the many types of lathes available, the CNC lathe stands out as one of the most advanced and precise. If you are in need of precision CNC lathe parts, then you need to partner with a reliable and experienced company, and latency is the perfect choice.At Lathe, we specialize in offering fast and accurate CNC turning services. Our lathe department is equipped with state-of-the-art CNC lathes and proven technology, positioning us to serve our customers' needs best. Our experienced and skilled machinists have the knowledge and training required to program even the most complex turning operations. As a result, we can produce highly precise parts while maintaining a fast turnaround time.Our lathes are equipped with cutting-edge technology that enables them to deliver exceptional accuracy, regardless of the complexity of the part. Additionally, our lathes have a range of spindle speeds, allowing us to handle a wide variety of materials, including aluminum, brass, copper, stainless steel, and more.We take quality seriously at Lathe, and we have put measures in place to ensure that our customers receive parts of the highest quality. First, we use state-of-the-art quality control equipment to verify that our parts meet the required specifications. Additionally, we have a team of experienced quality control technicians who conduct regular inspections to ensure that our parts meet our high-quality standards.We understand that time is of the essence in many manufacturing processes, which is why we are committed to offering fast turnaround times. Our efficient machining processes, combined with our team of skilled machinists, enable us to produce parts quickly and efficiently.In conclusion, if you are in need of precision CNC lathe parts, you need to partner with a reliable and experienced company. At Lathe, we have the equipment, technology, and skilled personnel required to deliver high-quality parts that meet your specifications. Contact us today to learn more about our CNC turning services and how we can help you with your manufacturing needs. And if you're searching for terms like "precision CNC lathe part", you can be sure that you've come to the right place.
Sheet Metal Bending Tools: Dies, Press Brakes, Tube & Wire Bending
Sheet metal bending is a process that involves creating a bend in a metal sheet to give it a certain shape or form. This process is done using specialized tools and equipment such as bending dies, press brakes, and tube & wire bending machines.Bending dies are the main tool used for sheet metal bending. They are used to apply force to the metal to create a bend. These dies come in different shapes and sizes depending on the shape and size of the bend required. The dies can be used with a stamping press or press brakes.Stamping presses are machines that are used to apply pressure to the metal sheet to create the desired shape. The press brake is another machine that is used for sheet metal bending. It is a large machine that uses a hydraulic system to apply force to the metal sheet. The press brake can create several bends in the metal sheet at once.There are several types of bending dies that can be used for sheet metal bending. The most common type of bending die is the progressive bending die. This die allows multiple bends to be created simultaneously, which makes the process faster and more efficient. Other types of bending dies include the wiping die, rotary die, and the air-bending die.Wire bending machines are used to create bends in wire or rod-shaped materials. These machines use specialized dies to create precise bends in the wire. The bending process is done using a combination of force and heat to create the desired shape.Tube bending machines are used for creating bends in tubes and pipes. These machines use mandrels and dies to create precise bends in the tube. The mandrel is a rod that is placed inside the tube to prevent it from collapsing during the bending process.When it comes to sheet metal bending, it is important to use the right tools and equipment to ensure that the sheet metal is bent correctly. Bending dies and tools are crucial in this process. With the right tools and equipment, it is possible to create precise bends that will meet the desired requirements.In conclusion, sheet metal bending is a complex process that requires specialized tools and equipment like bending dies, press brakes, tube & wire bending machines. Each of these pieces of equipment plays a crucial role in the bending process and is designed to create precise bends. When used correctly, these tools can help you achieve the desired shape and form for your sheet metal project.
Listen to a New Track called Spinning by an Artist on SoundCloud
article about a new sound dynamic software and its benefits for music producers.In today's music industry, the need to innovate and explore new ways of creating sounds has never been greater. While traditional software and hardware tools have their advantages, they can sometimes fall short when it comes to creating complex and dynamic sounds that stand out in today's crowded market. That's where the new sound dynamic software, developed by a leading audio software company, comes in.The new software, which has been in development for over two years, introduces a new way of creating soundscapes that is different from anything else on the market. Unlike traditional software which is linear, the new software is spherical in nature, allowing for a much greater degree of freedom when it comes to creating and manipulating sound.So how does it work? The software uses a series of spherical coordinates to create a three-dimensional soundscape. Sound sources can be added in any position, and the software allows for complete control over the distance, direction and intensity of each source. This means that music producers can create complex and dynamic soundscapes that are not limited by traditional linear software.The benefits of this new software are numerous. For one, it allows producers to create truly unique and immersive soundscapes that can help their music stand out in a crowded market. The spherical nature of the software also makes it much easier to work with than traditional linear software, as it allows producers to work with sounds in a more intuitive and natural way.Perhaps the biggest benefit of this new software, however, is in its ability to create truly dynamic soundscapes. Traditional software can sometimes struggle when it comes to creating sounds that change in intensity or direction over time. The new software, however, allows for complete control over every aspect of the soundscape, which means that producers can create sounds that evolve and change in ways that were simply not possible with traditional software.The development of this new software has been a long and arduous process, but the results speak for themselves. Industry insiders have been raving about the software, with many calling it a game-changer for the industry. Music producers who have had the chance to use the software have been equally impressed, with many saying that it has revolutionized the way they create sound.The new software is also highly customizable, allowing producers to tailor it to their specific needs. This means that it can be used in a wide variety of genres, from electronic dance music to classical orchestration. The software is also compatible with a wide range of hardware and software setups, making it a valuable addition to any producer's toolbox."It's amazing to think that just a few years ago, this kind of technology was simply not possible," said one industry insider. "But now, thanks to the hard work of this software company, we have a game-changing tool that is going to change the face of music production."Overall, the new sound dynamic software is a must-have for any music producer looking to create unique and dynamic soundscapes. It represents a significant leap forward in technology and is sure to be a game-changer for the industry.
Precision CNC Machining Services in Texas with Low Costs and Fast Lead Times
In the world of manufacturing, precision is paramount. The emergence of Computer Numerical Control (CNC) machines revolutionized the way manufacturers produced parts. CNC milling and turning are some of the most common machining processes, and with technological advancements, the processes have become more efficient, accurate, and cost-effective. 3D Hubs provides a CNC machining service in Texas that delivers low-cost, precision machined parts with an 8-day lead time from America, China, Europe, and India. CNC milling is a process that involves removing material from a workpiece using rotary cutters. The milling machine uses computer-aided design (CAD) to guide the cutting tool along different axes to achieve the desired shape. The machine can produce complex parts with a high level of precision and accuracy. The process is ideal for producing parts with intricate shapes, contours, and features that would be challenging to make using manual machining methods.CNC turning involves spinning a workpiece on a lathe machine while a cutting tool removes material to achieve the desired shape. The lathe machine uses CAD to guide the cutting tool along different axes. The process is ideal for producing round or cylindrical parts, including threads and grooves. Like CNC milling, the process is efficient and accurate, enabling the production of high-quality parts with tight tolerances.3D Hubs' CNC machining service in Texas utilizes both milling and turning processes to deliver high-precision, low-cost machined parts. The company uses computer-controlled machines that operate 24/7 to minimize lead times and reduce the cost of production. The machines are capable of machining a wide range of materials, including metals, plastics, and composites. The company's CNC milling machines use up to 5 axes, enabling the production of complex geometries with highly accurate finishes. The machines can produce parts with tolerances as tight as ± 0.005mm, ensuring that the parts meet the required specifications. The CNC turning machines, on the other hand, can produce parts with a diameter as small as 1mm and a length of up to 300mm. In addition to CNC milling and turning, 3D Hubs' CNC machining service in Texas includes finishing processes such as sandblasting, polishing, and anodizing. The finishing processes are essential to improve the appearance and functionality of the parts. Sandblasting, for instance, can give the parts a textured surface that improves their grip, while anodizing can enhance their corrosion resistance.3D Hubs' CNC machining service in Texas is ideal for businesses that require low-cost, high-precision machined parts. The company's ability to produce parts with tight tolerances, short lead times, and a wide range of materials makes it a valuable partner for manufacturers across different industries. The company's commitment to quality and customer satisfaction ensures that businesses get the best value for their money.In conclusion, CNC milling and turning are essential machining processes that have transformed the manufacturing industry. The processes are efficient, accurate, and cost-effective, making them ideal for producing high-quality parts with tight tolerances. 3D Hubs' CNC machining service in Texas utilizes these processes to deliver low-cost, high-precision machined parts with short lead times. With their commitment to quality and customer satisfaction, businesses can rely on 3D Hubs to provide the best value for their money.
How to Build a Heavy CNC Milling Machine: 18 Steps with Pictures
Machine, Instructables, heavy CNC milling, epoxy granite, linear guides, building processCNC Milling Machine: A Comprehensive Guide to Building Your OwnBuilding a heavy-duty CNC milling machine is not a task for the faint-hearted. It requires a lot of different working steps and careful planning to ensure that you end up with a machine that can deliver precise and accurate results. In this blog post, we will take a closer look at the steps involved in building a big CNC machine with good milling performance, as well as the materials and equipment needed for the project.Step 1: Design and PlanningThe first step in building a CNC milling machine is to design and plan the machine. This involves deciding on the size of the machine, the materials to be used, the type of milling machine to be used, and the features and capabilities that the machine should have. It is important to have a clear understanding of the requirements before starting the project to avoid any costly mistakes down the line.Step 2: Building the MoldThe next step is to build a big and accurate mold for casting the epoxy granite. Epoxy granite is a popular material for building milling machines due to its sturdiness and vibration damping properties. The mold should be designed to ensure that it is rigid and can create a smooth surface finish. The casting process should be done carefully to avoid any air bubbles or voids that can cause inaccuracies in the finished cast.Step 3: Aligning the Linear GuidesThe linear guides play a crucial role in the accuracy and precision of the milling machine. They are responsible for guiding the cutting tool along a straight and consistent path. The linear guides should be aligned carefully to ensure that they are in perfect alignment with the cutting tool. This requires careful attention to detail and the use of precision measuring tools.Step 4: Building the Machine FrameThe frame of the milling machine should be built to be strong and rigid. The use of high-quality materials such as aluminum or steel is recommended. The frame should be designed with sufficient clearance to accommodate the linear guides and other machine components.Step 5: Assembling the MachineOnce all the components of the milling machine have been prepared, it is time to start assembling the machine. This requires careful attention to detail and a lot of patience. Each component should be installed carefully and securely to ensure that the machine is stable and can deliver precise and accurate results.ConclusionBuilding a heavy CNC milling machine is a challenging task that requires a lot of time and effort. However, with careful planning and attention to detail, it is possible to build a machine that can deliver precise and accurate results. The use of high-quality materials and precision measuring tools is essential to ensure that the machine is built to the required specifications. With the right approach, anyone can build their own CNC milling machine and take their machining capabilities to the next level.
High Precision Vacuum Casting Filament for Consistent Layering and Easy Support Removal
and 3D printing.In today's fast-paced technological world, 3D printing has become increasingly popular, revolutionizing the way we design and create products. One of the key features of 3D printing is the new range of materials available which can produce high-quality and accurate printed products. Vaccum Casting is one such material that is perfect for the production of complex or intricate parts.Vaccum Casting is a thermoplastic elastomer that is commonly used in 3D printing. Its unique properties make it a perfect choice for printing objects that require precision and accuracy. With an extrusion temperature ranging from 175-200C, Vaccum Casting is an ideal option for printing small and delicate parts. The filament also has high roundness and precision of +/- 0.01 mm, ensuring that your print is accurate and of high quality.One of the key benefits of Vaccum Casting is that it sticks nicely to glass/kapton tape heated bed, resulting in no first-layer problem. This makes it easier to work with as it ensures that the print stays in place while printing. Additionally, the filament extrudes precisely for fast printing and consistent layering, which results in better prints overall.Filament comes in a light/compact spool, in a sealed package with a bag of desiccant, which ensures that the filament remains dry and of high quality. The desiccant is a moisture-absorbing material, which means that even if the filament is kept in a humid environment, it will not absorb the moisture and will be of high quality during printing.Another key benefit of Vaccum Casting is that it is easy to remove support material. When printing complex or intricate parts, support material is often required to ensure that the parts maintain their shape and structure. Vaccum Casting's easy-to-remove support material feature ensures that you can quickly and easily remove the material and finish your prints.In conclusion, Vaccum Casting is an excellent material for 3D printing, with its unique properties making it ideal for producing small and complex parts. Its high roundness and precision make it ideal for printing objects that require accuracy and precision. The ease of removing support material and the ability to stick nicely to a heated bed are other benefits that make Vaccum Casting a preferred option for 3D printing. So, if you're looking for a reliable and precise filament for 3D printing, be sure to try Vaccum Casting.
CNC Turning Services for High-Quality Lathe Turned Parts
Service, Lathe Turned Production Parts, Prototyping, CNC Machined Parts, Manufacturing Partners, Instant CNC Turning Quote.CNC Turning Service: Your One-Stop Solution for All Your Lathe NeedsIn today's fast-paced manufacturing industry, the demand for precision and accuracy in parts production is more important than ever. Thanks to advances in technology, the CNC turning service has emerged as the go-to solution for manufacturing high-quality lathe-turned production parts. CNC Turning, with its precision, speed, and flexibility, has revolutionized the world of manufacturing and has become an essential part of modern-day production processes.At CNC Turning Service, we understand the importance of getting it right the first time, which is why we offer an exceptional range of services dedicated to providing our clients with the best possible results. Our services provide complete end-to-end solutions, from prototyping to CNC machined parts, and we deliver them with unbeatable speed, quality, and price.Our Global Network of Certified Manufacturing PartnersCNC Turning Service is proud to have a global network of 25 certified manufacturing partners, enabling us to offer our clients the best CNC turning services available. These partners have over 100 CNC turning machines, allowing us to produce everything from simple to complex parts. Our partners undergo a rigorous selection process to ensure they meet our exacting standards of quality, consistency, and efficiency. As a result, our clients benefit significantly from increased savings, faster lead times, and access to a wider range of capabilities.The Most Cost-Effective Solution for PrototypingAt CNC Turning Service, we understand that prototyping is an essential part of the production process. As such, we offer our clients the most cost-effective solution for creating high-quality prototypes. Our CNC turning service gives our clients the ability to produce prototypes that are identical to the final product in terms of specifications, tolerances, and material, which reduces the risk of design errors and allows for necessary modifications before the final production.CNC Machined Parts With Unbeatable Quality and SpeedCNC Turning Service produces CNC machined parts with unbeatable speed and quality. Our partners' CNC turning machines produce precise and accurate parts with precise tolerances, finishes, and features. Whether you need single parts or thousands, our CNC turning service can provide you with the most efficient and cost-effective production.Instant CNC Turning QuoteCNC Turning Service offers an instant CNC turning quote to our clients. Our online quote system is user-friendly, simple, and straightforward to use. Our clients can upload their designs, specify their requirements, and receive a quote instantly. With our instant quote system, our clients can access real-time pricing information and plan their production processes accordingly.ConclusionAt CNC Turning Service, we provide our clients with a complete end-to-end solution for all their lathe-turned production parts needs. Our global network of certified manufacturing partners, our cost-effective prototyping solutions, and our unbeatable quality and speed in producing CNC machined parts, make us the go-to solution for manufacturing high-quality parts. Contact us today and experience the benefits of our CNC turning services.