What is Water-jet Technology and How Does it Work?
By:Admin
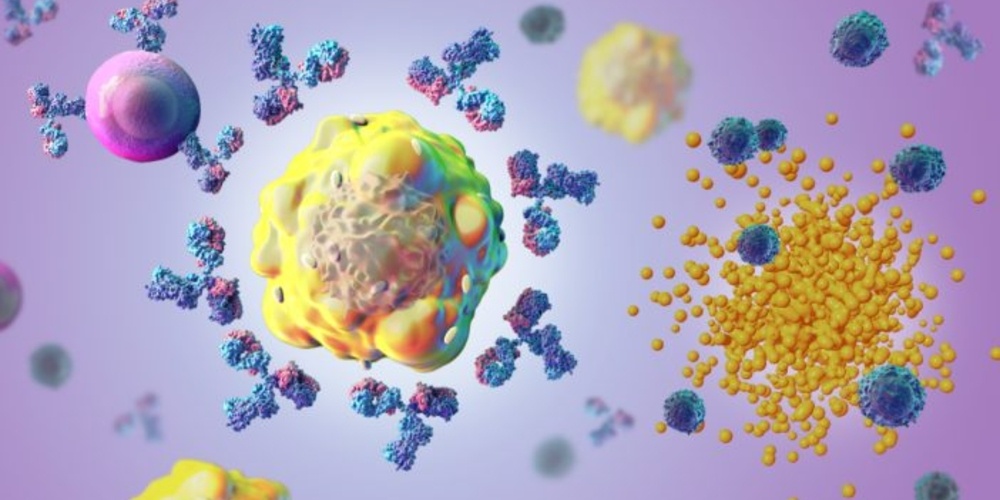
The process of water-jet cutting starts by using a high-pressure pump that pumps water through a nozzle, which produces a super-fast stream of water that is directed onto the material to be cut. The water pressure can be adjusted to suit the type of material being cut, from soft materials like plastic, rubber, and foam to hard materials like metals, ceramics, and glass.
One of the most significant benefits of water-jet technology is its ability to perform intricate cuts without creating heat-affected zones (HAZ). Thermal distortion, discoloration, and other undesirable effects are often seen when traditional cutting methods are used, like plasm cutting. However, water-jet cutting ensures material integrity through cold cutting, making it ideal for precision machining, intricate architectural designs, medical equipment, aerospace, and automotive parts.
Traditional cutting methods such as laser and plasma can produce toxic fumes or debris that can be dangerous to the environment and human health. In contrast, water-jet cutting is eco-friendly and safe. The water used in this process can be recycled and reused, and the cutting operation produces no hazardous waste, allowing companies to reduce their environmental footprint considerably.
Moreover, water-jet technology requires no special tooling, which means changing between different materials and designs is a breeze. This makes water-jet cutting an even more attractive option for manufacturers who need to switch between various production requirements quickly. Additionally, with advancements in technology, 5-axis cutting technology and robotics can be utilized, allowing greater flexibility and increased accuracy in cutting, ensuring more efficient and cost-effective production.
The benefits of water-jet technology are not limited to cutting and shaping applications, as it has other uses too. Water-jet cleaning is another application of this technology. It involves the use of high-pressure water streams to remove dirt and grime from surfaces, making it an effective cleaning option for many businesses. Cleaning using a water-jet is particularly useful in the food and beverage industry, where sanitation is critical.
Another advantage of using water-jet technology in cleaning is that it does not require any chemicals to aid the cleaning process. This, in turn, ensures that the cleaned surfaces are safe for human consumption, eliminating the need for chemical-based cleaning agents harmful to the environment and humans. The use of water-jet technology in cleaning can significantly reduce washing times and increase production efficiency, making it an ideal solution for many businesses.
In conclusion, water-jet technology presents an innovative and eco-friendly solution for many manufacturing and cleaning applications. Its benefits are unrivaled when compared to traditional cutting and cleaning technologies. From increased production efficiency to reduced environmental footprint to the ability to perform intricate and precise cuts, water-jet technology has fast become a sought-after option for many businesses looking to improve their bottom line. Companies that have not yet implemented this technology in their operations are urged to give it a try and discover the numerous cost and time-saving benefits it can offer.
Company News & Blog
Production-Grade 3D Printer Enables MTConnect Integration for Aerospace and Industrial Applications
, F900 3D printer, production applications, aerospace industry, MTConnect protocol.Additive manufacturing has revolutionized the manufacturing industry with the ability to create complex geometries with high precision and speed. One of the leading players in the additive manufacturing market is the F900 3D printer, designed for production applications in the aerospace industry and other high-performance industries. This blog discusses the latest development in the F900 3D printer, which now features an MTConnect-ready interface, offering enhanced connectivity and data exchange capabilities.The F900 3D printer is known for its high-performance capabilities, reliability, and large-scale printing. The printer uses the Fused Deposition Modeling (FDM) technology, which involves building 3D models layer by layer by depositing material in a melted state. The FDM technology provides a high degree of design flexibility, allowing the production of complex geometries without the need for additional machining or assembly processes.The F900 3D printer has been widely used in the aerospace industry for the production of complex parts, such as ducting, brackets, and housings. These parts require high precision and accuracy, and the F900 has proven to be a reliable and cost-effective solution for their manufacturing. Additionally, the F900 has been used in other industries, such as automotive, defense, and medical, where the demand for high-performance parts is also high.The latest development in the F900 3D printer is its integration with the MTConnect protocol. MTConnect is an open-source communication protocol used in manufacturing equipment to facilitate data exchange and collection. The protocol offers a standardized way of communicating machine data, making it easier to integrate different systems and devices.With its MTConnect-ready interface, the F900 3D printer can now connect to other manufacturing systems, such as Enterprise Resource Planning (ERP) systems, Manufacturing Execution Systems (MES), and other machines in the production line. This enables better coordination between different manufacturing processes, leading to higher efficiency and productivity. Additionally, the MTConnect protocol allows for real-time monitoring of the printing process, giving operators better control and visibility over the manufacturing process.The integration of the MTConnect protocol into the F900 3D printer is a significant step towards enhancing the connectivity and data sharing capabilities of the printer. This development enables the printer to be integrated into a broader manufacturing ecosystem, allowing for seamless data exchange and coordination between different systems. This integration is highly relevant in the aerospace industry, where the demand for high-performance parts is only increasing.In conclusion, the F900 3D printer is a high-performance system designed for production applications in the aerospace industry and other high-performance industries. With its latest development, the integration of the MTConnect protocol, the printer now offers enhanced connectivity and data exchange capabilities, making it easier to integrate into a broader manufacturing ecosystem. This development ensures the F900 3D printer remains one of the leading additive manufacturing systems in the market today.
How to Build a Heavy CNC Milling Machine: 18 Steps with Pictures
Machine, Instructables, heavy CNC milling, epoxy granite, linear guides, building processCNC Milling Machine: A Comprehensive Guide to Building Your OwnBuilding a heavy-duty CNC milling machine is not a task for the faint-hearted. It requires a lot of different working steps and careful planning to ensure that you end up with a machine that can deliver precise and accurate results. In this blog post, we will take a closer look at the steps involved in building a big CNC machine with good milling performance, as well as the materials and equipment needed for the project.Step 1: Design and PlanningThe first step in building a CNC milling machine is to design and plan the machine. This involves deciding on the size of the machine, the materials to be used, the type of milling machine to be used, and the features and capabilities that the machine should have. It is important to have a clear understanding of the requirements before starting the project to avoid any costly mistakes down the line.Step 2: Building the MoldThe next step is to build a big and accurate mold for casting the epoxy granite. Epoxy granite is a popular material for building milling machines due to its sturdiness and vibration damping properties. The mold should be designed to ensure that it is rigid and can create a smooth surface finish. The casting process should be done carefully to avoid any air bubbles or voids that can cause inaccuracies in the finished cast.Step 3: Aligning the Linear GuidesThe linear guides play a crucial role in the accuracy and precision of the milling machine. They are responsible for guiding the cutting tool along a straight and consistent path. The linear guides should be aligned carefully to ensure that they are in perfect alignment with the cutting tool. This requires careful attention to detail and the use of precision measuring tools.Step 4: Building the Machine FrameThe frame of the milling machine should be built to be strong and rigid. The use of high-quality materials such as aluminum or steel is recommended. The frame should be designed with sufficient clearance to accommodate the linear guides and other machine components.Step 5: Assembling the MachineOnce all the components of the milling machine have been prepared, it is time to start assembling the machine. This requires careful attention to detail and a lot of patience. Each component should be installed carefully and securely to ensure that the machine is stable and can deliver precise and accurate results.ConclusionBuilding a heavy CNC milling machine is a challenging task that requires a lot of time and effort. However, with careful planning and attention to detail, it is possible to build a machine that can deliver precise and accurate results. The use of high-quality materials and precision measuring tools is essential to ensure that the machine is built to the required specifications. With the right approach, anyone can build their own CNC milling machine and take their machining capabilities to the next level.
Discover the Best Stamping Tools and Beading Courses Online
and Bead Art’. Bead art has become increasingly popular over the past decade, reaching new levels of creativity and elegance. From bracelets, necklaces, and earrings to stunning home decor, beads offer a vast range of possibilities when it comes to crafting. There are numerous types of beads available in the market, each having its unique charm and quality. But, you may ask, how can you add that extra flavor to your bead art? Stamping tools can help!Stamping tools have been around for a long time and are usually used in leathercraft and metal stamping. However, they can be effectively used in creating bead art too. The technique brings out a new dimension in bead art and allows for a stylish and personalized touch.So, how do you use stamping tools in your bead art? For starters, you will need a few things: a set of stamping tools, a hammer, a workbench, and the beads that you want to stamp on. Once all these are in place, you can go ahead and start!First, you need to determine which stamping tool you want to use. There are various types of stamping tools available, including letters, numbers, and shapes. You can choose the alphabet stamping tool if you want to add a name or message onto your beads, or you could choose a pattern stamping tool to create a unique design on your beads.Once you have chosen the stamping tool, you can proceed to stamp the beads. Place the bead onto the workbench and position the stamping tool where you want it to be stamped. Then, gently tap the stamping tool with the hammer. Remember to be gentle as too much force could break the bead.Voila! You have added a personalized touch to your bead art. The possibilities are endless with stamping tools, and you can mix and match them to create unique designs on your beads.Bead It! iBEADS.com is an online store that offers classes in bead art and information about their two stores located in the island of Oahu. They have a vast range of beads and bead accessories available, including stamping tools. If you're a beginner or an experienced bead artist looking for inspiration, they offer classes catered to all levels.In conclusion, using stamping tools in bead art is an excellent way to add a personal flair to your jewelry pieces or home decor. With a little bit of creativity, you can come up with unique and stunning designs. Don't be afraid to experiment with different stamping tools and bead combinations – who knows, you might just discover your next masterpiece!
Custom Aluminium Extrusions for Your Specific Needs
In today's fast-paced and continuously developing modern world, businesses have to keep up with the growing needs of their clientele. One way to do that is through offering customized products, tailored to meet the specific requirements of the customer. Avocet Precision Metals has taken up that challenge, offering aluminum extrusion services that cater to the unique needs of the client.Avocet Precision Metals is a premier metals manufacturing company, located in the United Kingdom, known for its dedication to providing high-quality metal products and exceptional customer service. The firm utilizes cutting-edge technologies and equipment to provide unmatched precision in producing aluminum extrusions that meet the highest industry standards. With a workforce of highly skilled and experienced professionals well-versed in the latest practices of the extrusion industry, Avocet Precision Metals delivers results that surpass expectations.At its core, aluminum extrusion is a process by which manufacturers create complex shapes by forcing aluminum through a shaped opening. This process allows for customization of aluminum products to meet the exact specifications of clients. Avocet Precision Metals recognizes the importance of this process, making sure that all products conform to the customer's design, ensuring that products are manufactured to the highest quality standards.The company utilizes both hard and soft alloys of aluminum to match the specific requirements of the client. If the customer requires a particular combination of strength, corrosion resistance, and lightness, Avocet Precision Metals can deliver precisely what is needed. The company's aluminum extrusion services are highly versatile and can be used in a wide range of applications, including automotive, construction, machinery and much more.Avocet Precision Metals prides themselves in employing best practices, and quality measures to deliver the best customer experience. The company ensures that all the aluminum extrusion products are produced in an environmentally sustainable manner. The manufacturing process is regulated to ensure that it is as green as possible, minimizing the impact on the environment while ensuring that the customer receives high-quality products. Additionally, the company takes its customers' safety seriously and has worked hard to develop and implement safety and environmental protection policies.The high quality of the products that Avocet Precision Metals delivers is made possible by the company's continued investment in modern technology. This significantly reduces the production lead times and guarantees that the products are at the highest level of precision and quality. The company has installed cutting-edge CNC machines and presses that enable the team to manufacture high volumes of aluminum extrusions while reducing waste and maximizing efficiency.Avocet Precision Metals recognizes that customers have different budgets, and the company is always willing to work with clients to find a solution that works best for them. The company is committed to funding a team that supports its customers even after the sale is completed. They have an expert team of professionals on standby, ready to offer guidance and answer any queries that may arise.As a leading player in the aluminum extrusion industry, Avocet Precision Metals is continuously innovating and improving its processes to ensure they stay ahead of the competition. This continuous improvement mindset ensures that the company remains relevant in a market that is constantly changing. The firm's commitment to providing customers with the highest quality products and services has earned Avocet Precision Metals an excellent reputation among its customers and industry peers.In summary, Avocet Precision Metals is a top-tier manufacturer of aluminum extrusions that delivers high-quality and customized products according to clients' specifications. They are a company that prioritizes customer satisfaction and has invested in cutting-edge technology, skilled personnel, while staying environmentally conscious. These steps have enabled them to deliver on their promises while expanding their clientele base, and solidifying its position as a leading industry player.
Precision CNC Machining Services in Texas with Low Costs and Fast Lead Times
In the world of manufacturing, precision is paramount. The emergence of Computer Numerical Control (CNC) machines revolutionized the way manufacturers produced parts. CNC milling and turning are some of the most common machining processes, and with technological advancements, the processes have become more efficient, accurate, and cost-effective. 3D Hubs provides a CNC machining service in Texas that delivers low-cost, precision machined parts with an 8-day lead time from America, China, Europe, and India. CNC milling is a process that involves removing material from a workpiece using rotary cutters. The milling machine uses computer-aided design (CAD) to guide the cutting tool along different axes to achieve the desired shape. The machine can produce complex parts with a high level of precision and accuracy. The process is ideal for producing parts with intricate shapes, contours, and features that would be challenging to make using manual machining methods.CNC turning involves spinning a workpiece on a lathe machine while a cutting tool removes material to achieve the desired shape. The lathe machine uses CAD to guide the cutting tool along different axes. The process is ideal for producing round or cylindrical parts, including threads and grooves. Like CNC milling, the process is efficient and accurate, enabling the production of high-quality parts with tight tolerances.3D Hubs' CNC machining service in Texas utilizes both milling and turning processes to deliver high-precision, low-cost machined parts. The company uses computer-controlled machines that operate 24/7 to minimize lead times and reduce the cost of production. The machines are capable of machining a wide range of materials, including metals, plastics, and composites. The company's CNC milling machines use up to 5 axes, enabling the production of complex geometries with highly accurate finishes. The machines can produce parts with tolerances as tight as ± 0.005mm, ensuring that the parts meet the required specifications. The CNC turning machines, on the other hand, can produce parts with a diameter as small as 1mm and a length of up to 300mm. In addition to CNC milling and turning, 3D Hubs' CNC machining service in Texas includes finishing processes such as sandblasting, polishing, and anodizing. The finishing processes are essential to improve the appearance and functionality of the parts. Sandblasting, for instance, can give the parts a textured surface that improves their grip, while anodizing can enhance their corrosion resistance.3D Hubs' CNC machining service in Texas is ideal for businesses that require low-cost, high-precision machined parts. The company's ability to produce parts with tight tolerances, short lead times, and a wide range of materials makes it a valuable partner for manufacturers across different industries. The company's commitment to quality and customer satisfaction ensures that businesses get the best value for their money.In conclusion, CNC milling and turning are essential machining processes that have transformed the manufacturing industry. The processes are efficient, accurate, and cost-effective, making them ideal for producing high-quality parts with tight tolerances. 3D Hubs' CNC machining service in Texas utilizes these processes to deliver low-cost, high-precision machined parts with short lead times. With their commitment to quality and customer satisfaction, businesses can rely on 3D Hubs to provide the best value for their money.
Expert Thermal Management Consulting for High Performance Electronics
In the world of electronics, thermal management is one of the most important factors that can make or break the success of a product. When electronic circuits run, they generate heat, and if this heat is not properly dissipated, it can cause a range of problems, from degraded performance to component failure. This is where thermal management solutions come in, and Q ATS is a leading provider of such solutions.Founded with the aim of helping electronic product manufacturers bring their products to market faster, safer, and at a lower cost, Q ATS has established itself as a trusted partner for companies in a variety of industries. Whether it's designing a custom heatsink for a high-power LED light or analyzing the thermal performance of a data center, Q ATS has the expertise and experience to help clients solve their thermal management challenges.One of the key advantages of working with Q ATS is their comprehensive approach to thermal management analysis and design. Rather than simply offering off-the-shelf solutions, their team of engineers work closely with clients to understand the unique requirements of their products and design custom solutions that meet those needs. This ensures that clients get the best possible thermal performance for their products, while minimizing costs and time-to-market.Some of the services offered by Q ATS include thermal modeling and simulation, which allows them to predict the thermal performance of a product before it's even built. This can be especially valuable in applications where thermal management is critical, such as aerospace and defense. Q ATS also offers design and prototyping services, allowing clients to test and iterate on their thermal management solutions before committing to production.Another key area of expertise for Q ATS is the design and manufacture of heatsinks, which are a critical component in many electronic products. Heatsinks are used to dissipate heat from a component or circuit board to the surrounding air, and Q ATS can design heatsinks that are optimized for a specific application, providing maximum performance while minimizing weight and cost.In addition to their technical expertise, Q ATS is also committed to providing exceptional customer service. They work closely with clients throughout every stage of the project, from initial consultation to final delivery, ensuring that their needs are fully understood and met. Their team is highly responsive, with quick turnaround times and a willingness to go the extra mile to ensure client satisfaction.Overall, Q ATS is a valuable partner for any company looking to improve the thermal performance of their electronic products. With their comprehensive approach, technical expertise, and commitment to customer service, they can help clients get their products to market faster, safer, and more cost-effectively than ever before.
Listen to a New Track called Spinning by an Artist on SoundCloud
article about a new sound dynamic software and its benefits for music producers.In today's music industry, the need to innovate and explore new ways of creating sounds has never been greater. While traditional software and hardware tools have their advantages, they can sometimes fall short when it comes to creating complex and dynamic sounds that stand out in today's crowded market. That's where the new sound dynamic software, developed by a leading audio software company, comes in.The new software, which has been in development for over two years, introduces a new way of creating soundscapes that is different from anything else on the market. Unlike traditional software which is linear, the new software is spherical in nature, allowing for a much greater degree of freedom when it comes to creating and manipulating sound.So how does it work? The software uses a series of spherical coordinates to create a three-dimensional soundscape. Sound sources can be added in any position, and the software allows for complete control over the distance, direction and intensity of each source. This means that music producers can create complex and dynamic soundscapes that are not limited by traditional linear software.The benefits of this new software are numerous. For one, it allows producers to create truly unique and immersive soundscapes that can help their music stand out in a crowded market. The spherical nature of the software also makes it much easier to work with than traditional linear software, as it allows producers to work with sounds in a more intuitive and natural way.Perhaps the biggest benefit of this new software, however, is in its ability to create truly dynamic soundscapes. Traditional software can sometimes struggle when it comes to creating sounds that change in intensity or direction over time. The new software, however, allows for complete control over every aspect of the soundscape, which means that producers can create sounds that evolve and change in ways that were simply not possible with traditional software.The development of this new software has been a long and arduous process, but the results speak for themselves. Industry insiders have been raving about the software, with many calling it a game-changer for the industry. Music producers who have had the chance to use the software have been equally impressed, with many saying that it has revolutionized the way they create sound.The new software is also highly customizable, allowing producers to tailor it to their specific needs. This means that it can be used in a wide variety of genres, from electronic dance music to classical orchestration. The software is also compatible with a wide range of hardware and software setups, making it a valuable addition to any producer's toolbox."It's amazing to think that just a few years ago, this kind of technology was simply not possible," said one industry insider. "But now, thanks to the hard work of this software company, we have a game-changing tool that is going to change the face of music production."Overall, the new sound dynamic software is a must-have for any music producer looking to create unique and dynamic soundscapes. It represents a significant leap forward in technology and is sure to be a game-changer for the industry.
Find Top Quality Aluminum Extrusion Suppliers and Manufacturers
for Improved Durability and Aesthetic Appeal.Aluminum extrusions are widely used in various industries due to their versatility, strength, and lightweight properties. These extrusions are produced by pushing an aluminum billet through a die to create a specific cross-sectional shape. The end product is then used for various applications such as construction, automotive, aerospace, and consumer goods industries.Aluminum extrusions can be further enhanced by anodizing. Anodized aluminum extrusions have a protective layer of oxide coating on the surface, which results in improved durability and aesthetic appeal. This process involves immersing the aluminum extrusion into an acidic electrolyte bath and applying an electrical current to create an oxide layer on the surface. The thickness of the oxide layer can be controlled to achieve the desired level of protection and color.The benefits of anodized aluminum extrusions are numerous. Firstly, this process provides corrosion resistance, making it ideal for outdoor applications that are exposed to harsh weather conditions. Secondly, the oxide layer is hard and abrasion-resistant, improving the durability of the aluminum extrusion. Thirdly, anodized aluminum extrusions have a uniform color that is long-lasting and does not fade over time. This is particularly beneficial for products that require attractive finishes such as furniture, lighting fixtures, and consumer electronics.In addition to the practical benefits, anodized aluminum extrusions offer a range of aesthetic benefits. Anodizing can produce a variety of colors, from natural silver to shades of black, blue, and red. This makes it possible to create customized finishes for different applications. Anodized aluminum extrusions also have a matte or satin finish, which adds a touch of elegance to the end product.Anodized aluminum extrusions are produced by many manufacturers and suppliers listed on IQS Directory. These companies have the expertise and equipment to create high-quality anodized aluminum extrusions that meet customer specifications. The process of anodizing can be customized to achieve specific colors, thicknesses, and finishes. IQS Directory has a wide range of anodized aluminum extrusion suppliers that offer competitive prices and quick response times. This means that customers can get the products they need, when they need them.In conclusion, anodized aluminum extrusions offer a range of benefits that make them superior to other types of material. The process of anodizing improves durability, corrosion resistance, and aesthetic appeal. It also allows for customization of colors and finishes, making it ideal for various applications. IQS Directory has a vast network of anodized aluminum extrusion suppliers that offer top-quality products at affordable prices. For those looking for durable and attractive aluminum extrusions, anodizing is the answer.
China-Based Manufacturer Offers Precision CNC Machined Parts
Wintec Precision Machining Co., Ltd: Your One-Stop Solution for CNC Precision Machined ComponentsWintec Precision Machining Co., Ltd is a leading OEM/ODM manufacturer of CNC precision machined components in China. With years of experience in the industry, Wintec has emerged as a reliable and trustworthy machining partner for businesses across the globe. Our team of highly skilled engineers and technicians, along with state-of-the-art infrastructure and advanced technology, enable us to deliver high-quality machined products that are second to none.At Wintec, we operate with a customer-first approach where customer satisfaction is our top priority. We work closely with our clients to understand their specific requirements and offer customized solutions that meet their needs. We have an extensive range of machining capabilities, including CNC turning, CNC milling, and CNC grinding, to provide accurate and precise parts that meet our client's specifications.Our CNC precision machined components are made using strict quality control measures that ensure superior product performance and reliability. We use only the highest quality raw materials that are sourced from reputable suppliers to ensure that our products meet stringent industry standards. Our commitment to quality is demonstrated by our ISO 9001:2015 certification, a testament that we deliver quality products consistently.At Wintec, we offer a broad range of CNC precision machined components, including shafts, sleeves, gears, housings, and more. We specialize in producing quality parts that cater to a wide range of industries, including the automotive, aerospace, medical, and energy sectors. Our machining capabilities allow us to create parts with intricate designs, intricate surface finishes, and tight tolerances that meet our client's exacting requirements.As a China-based manufacturer, Wintec offers our clients a cost-effective solution that does not compromise on quality. We have an extensive network of suppliers that allows us to source the best raw materials at a competitive price, passing on the savings to our clients. Our commitment to delivering cost-effective solutions makes us an attractive partner for businesses looking to reduce their production costs without sacrificing quality.In conclusion, Wintec Precision Machining Co., Ltd is a reliable partner for businesses in need of CNC precision machined components. We offer quality products, customized solutions, and cost-effective services that meet our clients' requirements. Our commitment to customer satisfaction, quality, and integrity makes us the ideal choice for your machining needs. Contact us today to learn more about our products and services.
Discover the Advantages of In-House Metal Fabrication for Quality and Timely Delivery
Sheet Metal Panel Fabrication – The Ultimate Solution to All Metal Fabrication NeedsSheet metal fabrication has come a long way since its inception. It has become an indispensable part of various industries and is used extensively for a multitude of purposes. Be it aerospace, automotive, construction, or any other industry – sheet metal fabrication is crucial in all of them.Although there are numerous methods of sheet metal fabrication, sheet metal panel fabrication has gained immense popularity among manufacturers. The primary reason for its popularity is the accuracy and precision it offers while fabricating metal panels.Let's delve deeper into the aspects of sheet metal panel fabrication and understand how it can help manufacturers in their metal fabrication needs.What is Sheet Metal Panel Fabrication?Sheet metal panel fabrication is a process that involves cutting, folding, and shaping sheet metal into panels. These panels can be of various shapes and sizes, and the fabrication process can be customized as per the requirement.Sheet metal panel fabrication involves using various tools such as laser cutting machines, CNC punching machines, and hydraulic press brakes. These machines are highly efficient and can provide accurate and precise output with utmost consistency.Advantages of Sheet Metal Panel Fabrication1. Precision – As stated earlier, sheet metal panel fabrication provides a high degree of precision and accuracy. The cutting and folding are done with utmost care and attention to detail, ensuring that the metal panels meet the required specifications.2. Customization – Sheet metal panel fabrication can be customized to cater to the specific needs of the manufacturer. This versatility allows manufacturers to produce metal panels of various shapes, sizes, and thicknesses. This flexibility is not present in other methods of metal fabrication.3. Efficiency – Sheet metal panel fabrication is highly efficient and can deliver output at a much quicker rate than other methods of metal fabrication. The use of advanced machines enhances the efficiency of the process, making it an ideal choice for manufacturers who want to increase their production speed.4. Cost-Effective – Sheet metal panel fabrication can be cost-effective in the long run. The high degree of precision and accuracy results in minimal wastage of material, making it a cost-effective method for manufacturers who want to cut down on their raw material costs.ConclusionSheet metal panel fabrication has become an integral part of various industries. It offers precision, customization, efficiency, and cost-effectiveness, making it the ultimate solution for all metal fabrication needs. If you want to streamline your metal fabrication process and improve your production speed, sheet metal panel fabrication is an ideal choice.So, if you are looking for a reliable metal fabrication service provider, look no further than sheet metal panel fabrication experts. They can help you with all your metal fabrication needs, ensuring that the end product meets your specifications.