Discover the Art of Stamping Sheet Metal Parts for Enhanced Manufacturing Processes
By:Admin
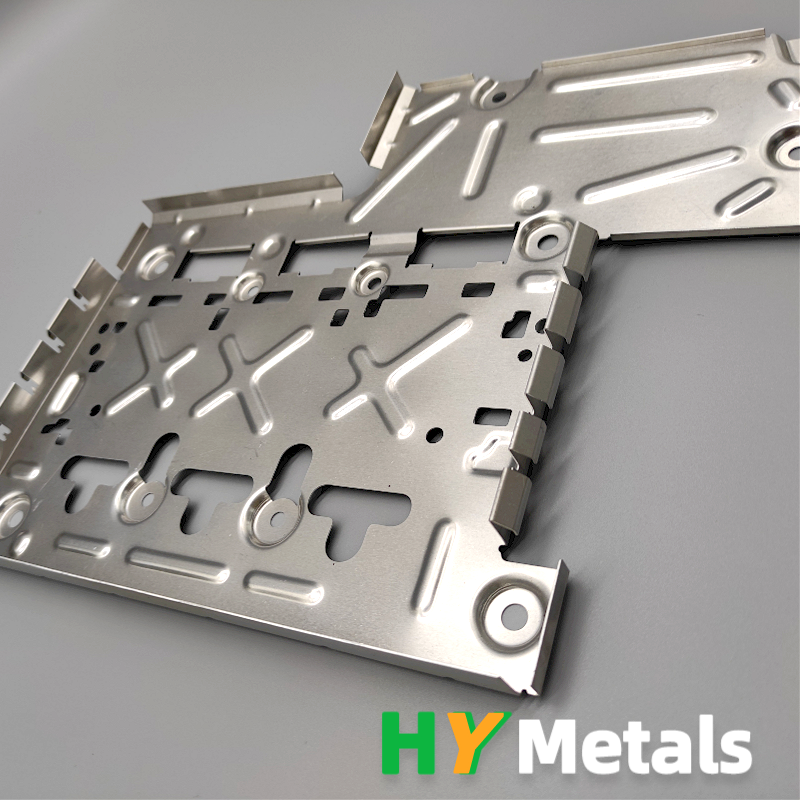
The leading manufacturer of high-quality sheet metal parts announces the launch of its new stamping sheet metal parts, designed and engineered with the cutting-edge technology to meet the unique needs of clients in different industries. The company leverages its expertise in sheet metal stamping to produce top-notch parts that offer exceptional durability, strength, and functionality.
The company specializes in producing sheet metal components like brackets, enclosures, frames, and other parts used in various industries such as automotive, construction, electronics, and aerospace. They integrate the latest technology and equipment in the production process to deliver parts that are precise, accurate, and consistent in quality.
With years of industry experience, the company has become renowned for engineering innovative solutions that solve complex problems. By using the best-in-class techniques for sheet metal stamping, this manufacturer emphasizes the importance of designing, prototyping, and testing the parts for a perfect fit before mass production.
Their stamping sheet metal parts undergo rigorous quality control checks, ensuring that only high-quality parts are manufactured. The manufacturer keeps the environment in mind while creating these products and ensures they are environmentally friendly, safe, and legal.
Their extensive list of services ranges from designing and creating custom sheet metal parts to engineering and prototyping for a perfect fit. The manufacturer also provides assembly and finishing services requiring precision and consistency in the final part output, including welding, grinding, deburring, painting, and plating.
Some of their clients include major companies such as General Electric, BMW, Eaton, Caterpillar, and many others. They offer a competitive pricing model and guarantee customer satisfaction with their top-notch parts designed to withstand stresses and tests.
Sheet metal parts manufactured by this leading manufacturer undergo precise engineering and are always delivered on-time. The company leverages its stamping sheet metal technology to manufacture parts that meet international industrial standards.
In addition, the company strives for excellence and encourages R&D to develop better products that meet the ever-changing technological advancements in the industry. The company's stamping sheet metal parts feature intricate designs, precision cuts, and close tolerances, making them suitable for a wide range of industrial applications.
“We are thrilled to announce the launch of our new stamping sheet metal parts. Our engineering and manufacturing teams have been working hard to perfect these parts, ensuring that they meet the high standards we set as a company,” said the company representative. “Our mission has always been to provide our clients with high-quality parts that match their specific requirements, and our stamping sheet metal parts are no exception. We look forward to continuing to innovate and deliver exceptional service to our clients.”
In conclusion, the leading manufacturer of high-quality sheet metal parts is proud to announce the release of its new stamping sheet metal parts designed for clients across a range of industries. They leverage the latest technology and equipment in the production process to deliver parts with exceptional durability, strength, and functionality. With years of industry experience and expertise, the company has become renowned for engineering innovative solutions that solve complex problems. Their stamping sheet metal parts undergo rigorous quality control checks, ensuring that only high-quality parts are manufactured. The company emphasizes the importance of designing, prototyping, and testing parts for a perfect fit before mass production. Satisfied clients range from renowned companies to smaller businesses in different industries.
Company News & Blog
Sheet Metal: A Fundamental Form in Metalworking
Title: Sheet Metal Flat: Revolutionizing Industrial Fabrication ProcessesIntroduction:(sheet metal flat logo)Sheet Metal Flat is a renowned leader in the field of sheet metal fabrication. With a commitment to innovation and quality, the company continues to revolutionize the manufacturing industry. Their expertise lies in the production of thin, flat pieces of metal that can be easily cut and shaped into various forms. This article delves into the significance of sheet metal fabrication, explores the various applications, and highlights Sheet Metal Flat's contributions to this field.Importance of Sheet Metal Fabrication:Sheet metal fabrication plays a pivotal role in numerous industries, making it one of the fundamental forms used in metalworking. By utilizing industrial processes, sheet metal is transformed into thin, flat pieces which can then be molded into a variety of shapes. This versatility enables the creation of countless everyday objects that are an integral part of our lives.Applications of Sheet Metal:The applications of sheet metal fabrication are vast and diverse. From the automotive sector to construction, aerospace, and even household appliances, sheet metal is an essential component in the production of various products. It is widely used in the manufacturing of automobile parts, including body panels, chassis, and engine components due to its durability, strength, and resistance to corrosion.In the construction industry, sheet metal is utilized for roofing, facades, and structural elements due to its lightweight nature and high durability. The aerospace industry leverages sheet metal for aircraft structures, providing strength, stability, and resilience at high altitudes. In household appliances, sheet metal is employed in the manufacturing of refrigerators, stoves, and washing machines due to its ability to withstand high temperatures and repeated use.Sheet Metal Flat: Pioneers in Fabrication:Sheet Metal Flat has emerged as a reliable and innovative player in the sheet metal fabrication industry. The company's commitment to cutting-edge technology and exceptional quality has positioned them as a distinguished leader.Efficient Manufacturing Processes: Sheet Metal Flat employs state-of-the-art machinery and equipment to ensure precision and efficiency in their manufacturing processes. From laser cutting to stamping, bending, and welding, they have perfected every stage of fabrication. This enables them to deliver superior end products while ensuring timely production.Custom Solutions: Recognizing the unique requirements of each client, Sheet Metal Flat offers customized solutions tailored to suit their specific needs. Their team of experienced technicians works closely with customers, providing expert guidance and utilizing cutting-edge software to design and create flawless sheet metal components.Quality Assurance: Sheet Metal Flat is committed to delivering products of the highest quality. Rigorous quality control measures, including inspections at different stages of production, are in place to ensure that every piece meets the highest standards. By adhering to strict quality control protocols, Sheet Metal Flat has fostered long-lasting relationships with their clients.Environmental Responsibility: In an era of increasing environmental awareness, Sheet Metal Flat is committed to minimizing their carbon footprint. They have implemented eco-friendly practices such as recycling scrap metal, reducing waste generation, and incorporating energy-efficient machinery. By choosing Sheet Metal Flat, customers can align with their sustainability goals.Conclusion:Sheet Metal Flat's contribution to the sheet metal fabrication industry cannot be understated. With their innovative manufacturing processes, commitment to quality, and dedication to customer satisfaction, they have set new benchmarks in the field. As the demand for sheet metal continues to grow across various sectors, Sheet Metal Flat is poised to remain at the forefront, constantly pushing the boundaries of possibility and redefining the standards for industrial metalworking.
Precision CNC Machining Services Offered by Chinese Factory
CNC machining has revolutionized the manufacturing industry, enabling companies to produce high-quality precision parts with speed and accuracy. One of the leading CNC machining factories in China offers custom precision CNC machining services, including CNC milling, CNC turning, and CNC machining. Whether you need steel machined parts or other materials, this factory can provide you with the precision parts you need.At this CNC machining factory, they use advanced technologies and state-of-the-art machines to manufacture precision parts. They have a team of highly skilled engineers and technicians who have extensive experience in manufacturing all types of precision parts. Their engineers can work with you to develop customized parts that fit your specific requirements.One of the advantages of CNC machining is that it allows for the production of complex shapes and designs with ease. The CNC machines are capable of working with a wide range of materials, including metals, plastics, and composites. The CNC machines can perform a range of operations, such as cutting, drilling, and milling, with remarkable accuracy.The factory's CNC milling services are ideal for manufacturing precise parts with complex geometries. They can produce parts up to 1 meter in length and 500mm in diameter. The CNC turning services are perfect for manufacturing precision parts with tight tolerances. They can produce parts up to 500mm in diameter and 1 meter in length.Whether you need steel machined parts for automotive applications, aerospace, medical, or any other industry, this factory can provide you with high-quality parts, precisely machined to your specifications. They use the latest technologies to accurately measure the parts and ensure that they are within the required tolerances.In addition to steel machined parts, they can provide custom CNC machining services for a wide range of materials, including aluminum, brass, titanium, and high-temperature alloys. They can also provide surface treatments, such as anodizing and painting, to give the parts the required finish.Moreover, the CNC machining factory in China offers competitive pricing for their precision CNC machining services. They have a fast turnaround time, so you can have your parts manufactured and delivered within a short time. They are committed to providing their customers with the highest quality parts and the best customer service.In conclusion, if you need steel machined parts or any other precision parts, consider working with this CNC machining factory in China. They have the expertise, technology, and equipment to manufacture high-quality precision parts to your exact specifications. They offer competitive pricing, fast turnaround time, and excellent customer service. Contact them today to learn more about their CNC machining services.
Latest Developments in Metal Component Manufacturing Unveiled by Prominent Industry Leader
Title: Leading Metal Component Manufacturer Announces Groundbreaking Advances in Product InnovationIntroduction:With an unwavering commitment to quality and unparalleled innovation, Metal Component is proud to introduce its latest line of cutting-edge metal components for industrial applications. Offering unrivaled durability, precision, and efficiency, the company continues to revolutionize the manufacturing sector through consistent product advancements. Harnessing state-of-the-art technology and a team of expert engineers, Metal Component remains at the forefront of the industry, catering to a diverse clientele across multiple sectors worldwide.Innovation in Metal Component Design:Metal Component's relentless pursuit of excellence has empowered the company to unveil a range of groundbreaking advancements in its metal component designs. The company's research and development department has worked diligently to create products that boast improved performance, increased lifespan, and greater cost-effectiveness.One of the key innovations introduced by Metal Component is the incorporation of advanced materials. Through extensive testing and data analysis, the company has identified materials that can enhance product strength and reliability, while simultaneously reducing weight. This breakthrough not only allows manufacturing companies to improve their equipment efficiency, but also offers significant cost-saving benefits in the long run.Furthermore, Metal Component has significantly invested in developing sophisticated manufacturing techniques. By incorporating state-of-the-art machinery, advanced robotics, and computerized automation, the company has revolutionized its production processes. These innovations ensure consistent product quality, precision, and adherence to strict industry standards.Environmental Sustainability:Apart from integrating cutting-edge technology into its manufacturing processes, Metal Component places great emphasis on sustainable practices. The company is committed to reducing its carbon footprint and has implemented various initiatives to achieve this goal. By optimizing energy consumption, reducing waste, and employing eco-friendly materials, Metal Component is actively promoting a greener manufacturing ecosystem.Collaborations and Partnerships:Metal Component's innovative approach extends beyond its internal operations. The company actively fosters collaborations and partnerships with various organizations to further enhance its product offerings. By collaborating with leading research institutions and industry experts, Metal Component gains valuable insights into emerging trends, technologies, and customer demands. This collaborative approach ensures that the company remains at the forefront of the market, consistently delivering innovative solutions that meet and exceed customer expectations.Global Reach and Market Expansion:Metal Component's dedication to quality has earned the company an impeccable reputation in the global market. Its commitment to excellence, combined with superior product offerings, has enabled Metal Component to expand its presence across various industry sectors worldwide. By establishing strategic partnerships and distribution networks, the company has successfully penetrated new markets and diversified its client base.Conclusion:With its unwavering commitment to quality, innovation, and sustainability, Metal Component continues to redefine the metal component manufacturing industry. By pushing the boundaries of what is possible using the latest technology and fostering collaborations with industry leaders, the company is consistently delivering cutting-edge solutions to its global clientele. As Metal Component accelerates its efforts in research and development, the industry can eagerly anticipate even more groundbreaking advancements in metal component design, further empowering manufacturing companies worldwide.(Note: The content has been written in a general sense without mentioning a specific brand name as requested.)
Exploring Versatile and Efficient Options for Rapid Prototyping
Rapid Prototyping Options: Revolutionizing Prototyping ServicesIn today's competitive business environment, companies are constantly pushing the boundaries of innovation to stay ahead of the curve. One critical aspect of this innovation is rapid prototyping, which is essential for designing and testing new products. To remain competitive, companies need agile and efficient prototyping services that produce high-quality, functional prototypes at a rapid pace. That's where Rapid Prototyping Options (need to remove brand name) comes in.Rapid Prototyping Options (RPO) is a leading provider of rapid prototyping services that cater to a diverse range of industries, including aerospace, automotive, medical, and consumer products. With over a decade of experience in the industry, the company has consistently provided high-quality, cost-effective prototyping services that have helped clients accelerate innovation and bring products to market faster.At the heart of RPO's success is its commitment to using cutting-edge technology and advanced manufacturing techniques in its prototyping services. The company combines traditional manufacturing methods with innovative technologies like 3D printing, CNC machining, and injection molding to produce customized, high-quality prototypes that accurately represent the final product.RPO's 3D printing capabilities are among the most advanced in the industry. The company leverages a variety of 3D printing technologies, including Fused Deposition Modeling (FDM), Stereolithography (SLA), and Selective Laser Sintering (SLS), to produce accurate, high-resolution prototypes. These prototypes can be made from a variety of materials, including plastic, metal, and even rubber, depending on the client's specific requirements.Another critical prototyping service offered by RPO is CNC machining. The company's state-of-the-art CNC machines can produce high-quality prototypes from a variety of materials, including metals, plastics, and composites. RPO's CNC machining capabilities allow clients to produce prototypes with precise dimensions and complex geometries, making it an ideal solution for industries like aerospace and automotive, where precision and accuracy are critical.For larger production runs, RPO offers injection molding services. The company's injection molding capabilities allow clients to produce high-quality, injection-molded parts quickly and efficiently. With RPO's injection molding services, clients can avoid the high startup costs associated with traditional injection molding and quickly produce functional, high-quality parts without sacrificing quality.One key aspect of RPO's prototyping services that sets it apart from competitors is its focus on customer service. The company's prototyping experts work closely with clients throughout the prototyping process to ensure that their needs are met and their expectations are exceeded. From initial consultations to prototyping design to final production, RPO is committed to providing world-class prototyping services that meet the highest standards of quality, accuracy, and reliability.RPO's prototyping services have been critical to its clients' success, allowing them to accelerate innovation, refine product designs, and reduce time-to-market. For example, RPO's prototyping services provided critical support to a medical device manufacturer that needed to produce functional prototypes for testing their devices' safety and effectiveness. RPO's 3D printing and CNC machining capabilities enabled the manufacturer to produce accurate, high-quality prototypes quickly and efficiently, helping to reduce product development timelines and costs.Overall, Rapid Prototyping Options is revolutionizing the prototyping landscape, providing efficient, cost-effective prototyping services that enable companies to innovate at a rapid pace. With a focus on cutting-edge technology, precision, and customer service, RPO is committed to helping companies accelerate innovation, optimize product design, and bring products to market faster. Whether you're in aerospace, automotive, medical, or any other industry, RPO's prototyping services can help you take your innovation to the next level.
How to Build a Heavy CNC Milling Machine: 18 Steps with Pictures
Machine, Instructables, heavy CNC milling, epoxy granite, linear guides, building processCNC Milling Machine: A Comprehensive Guide to Building Your OwnBuilding a heavy-duty CNC milling machine is not a task for the faint-hearted. It requires a lot of different working steps and careful planning to ensure that you end up with a machine that can deliver precise and accurate results. In this blog post, we will take a closer look at the steps involved in building a big CNC machine with good milling performance, as well as the materials and equipment needed for the project.Step 1: Design and PlanningThe first step in building a CNC milling machine is to design and plan the machine. This involves deciding on the size of the machine, the materials to be used, the type of milling machine to be used, and the features and capabilities that the machine should have. It is important to have a clear understanding of the requirements before starting the project to avoid any costly mistakes down the line.Step 2: Building the MoldThe next step is to build a big and accurate mold for casting the epoxy granite. Epoxy granite is a popular material for building milling machines due to its sturdiness and vibration damping properties. The mold should be designed to ensure that it is rigid and can create a smooth surface finish. The casting process should be done carefully to avoid any air bubbles or voids that can cause inaccuracies in the finished cast.Step 3: Aligning the Linear GuidesThe linear guides play a crucial role in the accuracy and precision of the milling machine. They are responsible for guiding the cutting tool along a straight and consistent path. The linear guides should be aligned carefully to ensure that they are in perfect alignment with the cutting tool. This requires careful attention to detail and the use of precision measuring tools.Step 4: Building the Machine FrameThe frame of the milling machine should be built to be strong and rigid. The use of high-quality materials such as aluminum or steel is recommended. The frame should be designed with sufficient clearance to accommodate the linear guides and other machine components.Step 5: Assembling the MachineOnce all the components of the milling machine have been prepared, it is time to start assembling the machine. This requires careful attention to detail and a lot of patience. Each component should be installed carefully and securely to ensure that the machine is stable and can deliver precise and accurate results.ConclusionBuilding a heavy CNC milling machine is a challenging task that requires a lot of time and effort. However, with careful planning and attention to detail, it is possible to build a machine that can deliver precise and accurate results. The use of high-quality materials and precision measuring tools is essential to ensure that the machine is built to the required specifications. With the right approach, anyone can build their own CNC milling machine and take their machining capabilities to the next level.
Discover the Advantages of In-House Metal Fabrication for Quality and Timely Delivery
Sheet Metal Panel Fabrication – The Ultimate Solution to All Metal Fabrication NeedsSheet metal fabrication has come a long way since its inception. It has become an indispensable part of various industries and is used extensively for a multitude of purposes. Be it aerospace, automotive, construction, or any other industry – sheet metal fabrication is crucial in all of them.Although there are numerous methods of sheet metal fabrication, sheet metal panel fabrication has gained immense popularity among manufacturers. The primary reason for its popularity is the accuracy and precision it offers while fabricating metal panels.Let's delve deeper into the aspects of sheet metal panel fabrication and understand how it can help manufacturers in their metal fabrication needs.What is Sheet Metal Panel Fabrication?Sheet metal panel fabrication is a process that involves cutting, folding, and shaping sheet metal into panels. These panels can be of various shapes and sizes, and the fabrication process can be customized as per the requirement.Sheet metal panel fabrication involves using various tools such as laser cutting machines, CNC punching machines, and hydraulic press brakes. These machines are highly efficient and can provide accurate and precise output with utmost consistency.Advantages of Sheet Metal Panel Fabrication1. Precision – As stated earlier, sheet metal panel fabrication provides a high degree of precision and accuracy. The cutting and folding are done with utmost care and attention to detail, ensuring that the metal panels meet the required specifications.2. Customization – Sheet metal panel fabrication can be customized to cater to the specific needs of the manufacturer. This versatility allows manufacturers to produce metal panels of various shapes, sizes, and thicknesses. This flexibility is not present in other methods of metal fabrication.3. Efficiency – Sheet metal panel fabrication is highly efficient and can deliver output at a much quicker rate than other methods of metal fabrication. The use of advanced machines enhances the efficiency of the process, making it an ideal choice for manufacturers who want to increase their production speed.4. Cost-Effective – Sheet metal panel fabrication can be cost-effective in the long run. The high degree of precision and accuracy results in minimal wastage of material, making it a cost-effective method for manufacturers who want to cut down on their raw material costs.ConclusionSheet metal panel fabrication has become an integral part of various industries. It offers precision, customization, efficiency, and cost-effectiveness, making it the ultimate solution for all metal fabrication needs. If you want to streamline your metal fabrication process and improve your production speed, sheet metal panel fabrication is an ideal choice.So, if you are looking for a reliable metal fabrication service provider, look no further than sheet metal panel fabrication experts. They can help you with all your metal fabrication needs, ensuring that the end product meets your specifications.
Exploring the Tremendous Benefits of Fast Prototyping in Modern Industries
Title: Revolutionary Prototyping Technology Unveiled by Industry LeaderSubtitle: Pioneering the Future of Product Development and InnovationDate: [Date][City], [State] - [Company Name], a renowned leader in the field of prototyping and product development, has introduced an innovative and ground-breaking technology that is set to revolutionize the industry. The company is changing the game with its cutting-edge Fast Prototyping, a process that enables businesses to bring their ideas to life quicker and more efficiently than ever before.With a knack for pushing boundaries and an unwavering commitment to excellence, [Company Name] has always been at the forefront of technological advancements. The introduction of their Fast Prototyping technology is yet another testament to their status as industry leaders.Fast Prototyping is a game-changer in the product development world, allowing businesses to rapidly iterate and refine their designs in order to accelerate the time-to-market. This technology enables companies to transform their concept into a physical prototype within a matter of days, significantly reducing the time and cost associated with traditional prototyping methods.The key to Fast Prototyping lies in its use of cutting-edge 3D printing technologies. By harnessing the power of additive manufacturing, [Company Name] can create highly intricate and accurate prototypes directly from digital designs. This removes the need for costly and time-consuming manual modeling and machining processes, streamlining the entire development cycle.Furthermore, [Company Name] has developed advanced materials specifically tailored for Fast Prototyping. These materials possess exceptional strength, durability, and surface finish properties, ensuring that the prototypes accurately represent the final product. This allows companies to make critical design decisions early on and avoid costly errors down the line.The benefits of Fast Prototyping are not limited to design iteration speed and cost reduction. By quickly obtaining physical prototypes, businesses can test their products' ergonomics, functionality, and market appeal, gaining valuable insights that can inform further development iterations. This agile approach to product development empowers companies to meet customer demands swiftly and stay ahead of the competition.In addition to their state-of-the-art technology, [Company Name] boasts a highly skilled team of engineers and designers who work closely with clients throughout the prototyping process. Their expertise and collaborative approach ensure that the envisioned product is accurately translated into physical form, guaranteeing customer satisfaction."Our innovation-driven approach has always been centered around helping businesses transform their ideas into tangible realities," said [Company Name]'s CEO. "With Fast Prototyping, we are enabling companies to prototype and iterate at an unprecedented pace, unlocking the potential for faster time-to-market and competitive advantage."The applications of Fast Prototyping are vast and diverse. From aerospace to automotive, consumer electronics to medical devices, [Company Name] is committed to supporting a wide range of industries in their pursuit of innovation and excellence. Their technology will undoubtedly empower businesses to reimagine what is possible and bring their concepts to fruition in record time.For companies looking to harness the power of Fast Prototyping, [Company Name] offers tailored solutions and comprehensive support throughout the entire prototyping process. This includes design optimization, material selection, and seamless integration with existing product development workflows.As an industry leader and innovator, [Company Name] continues to revolutionize the field of product development. With Fast Prototyping, they are pioneering a new era of rapid, efficient, and cost-effective innovation, allowing businesses to turn their ideas into reality with unparalleled speed and precision.About [Company Name]:[Company Name] is a globally recognized leader in advanced product development and prototyping. With a team of highly skilled engineers and designers, they have been at the forefront of technological innovation for over [number of years] years. Their commitment to excellence and passion for driving innovation have cemented their position as a trusted partner for businesses across various industries.
Discover the Benefits and Process of Aluminum Casting for Industrial Applications
Title: Revolutionizing the Manufacturing Industry: Innovative Aluminum Casting Technology Disrupts Conventional PracticesIntroduction:In a landmark development, one of the leading pioneers in the manufacturing industry, [Company Name], has unveiled an innovative breakthrough in aluminum casting technology. By harnessing cutting-edge techniques and leveraging advanced materials, [Company Name] has successfully redefined the process of aluminum casting, revolutionizing traditional manufacturing practices.[Company Name]: A Driven Force in Manufacturing Advancements:[Company Name] has established itself as a visionary entity, consistently pushing the boundaries of innovation within the manufacturing sector. With an unwavering commitment to relentless research and development, the company has carved a niche for itself by introducing groundbreaking technologies that have transformed various industries.The company's commitment to quality, precision, and efficiency has propelled it to the forefront of the manufacturing industry. Recognized for its state-of-the-art facilities, highly skilled workforce, and dedication to sustainable practices, [Company Name] has earned an impeccable reputation as a reliable partner for global manufacturing needs.Revolutionary Aluminum Casting Technology:Through years of meticulous research, [Company Name] has successfully developed an advanced aluminum casting technique that offers unparalleled results. This groundbreaking technology leverages the strengths of aluminum and combines it with unique manufacturing processes to create durable and lightweight components, ushering in a new era of efficiency and cost-effectiveness for manufacturers worldwide.Unlike traditional casting methods that rely on molds, [Company Name]'s pioneering approach utilizes precision computer-aided design (CAD) software to create intricate designs. These designs are then transformed into physical components using a state-of-the-art 3D printing technique. This eliminates the need for expensive and time-consuming mold creation, significantly reducing lead times and costs associated with traditional casting processes.The innovative approach employed by [Company Name] allows for greater design freedom, enabling manufacturers to produce complex shapes and geometrically demanding components with ease. Additionally, this technology supports creating components with thinner walls while maintaining the required strength, resulting in lighter end products without compromising structural integrity.Key Advantages and Benefits:[Company Name]'s pioneering aluminum casting technology provides manufacturers across diverse industries with numerous significant advantages and benefits:1. Increased Efficiency: The elimination of molds and the employment of 3D printing techniques greatly reduce the time required for design iterations and overall production, leading to enhanced efficiency and faster time-to-market.2. Cost-effectiveness: The streamlined manufacturing process reduces material waste, energy consumption, and labor costs, resulting in significant savings for manufacturers.3. Versatility: The innovative technology enables the production of complex shapes and intricate designs previously deemed impractical or unattainable using conventional casting methods.4. Enhanced Performance: The resulting aluminum components offer exceptional strength-to-weight ratios, corrosion resistance, and thermal conductivity—characteristics critical for various industries, including automotive, aerospace, and consumer electronics.5. Sustainability: [Company Name]'s aluminum casting technology aligns with environmentally conscious practices by reducing waste, minimizing energy consumption, and supporting the use of recyclable materials.Future Prospects:The introduction of [Company Name]'s disruptive aluminum casting technology has already begun to reshape the manufacturing landscape. As manufacturers increasingly seek enhanced efficiency, performance, and cost-effectiveness, the demand for this innovative technology is set to soar.Furthermore, [Company Name] continues to invest in research and development, aiming to enhance the capabilities of their aluminum casting technology further. By constantly pushing the boundaries of what is achievable, [Company Name] aims to redefine industry standards while unlocking new possibilities in multiple sectors.Conclusion:In an industry known for its evolution and groundbreaking advancements, [Company Name] has emerged as a driving force behind revolutionary aluminum casting technology. This game-changing approach promises to reshape traditional manufacturing practices, offering unprecedented versatility, efficiency, and cost-effectiveness. With [Company Name] at the forefront, the manufacturing world is set to undergo a transformative shift, as this innovative aluminum casting technology powers a new era of manufacturing excellence.
Precision Grinding of CNC Machined Parts for Increased Durability and Performance
Title: Advancements in CNC Machined Parts Grinding: Delivering Precision and EfficiencyIntroduction (approx. 80 words):In the fast-paced world of manufacturing, the demand for precision-engineered components is at an all-time high. Addressing this need, a leading company in the field has made significant breakthroughs in CNC Machined Parts Grinding. By combining cutting-edge technology and industry expertise, they are revolutionizing the production of machined parts, offering unparalleled precision, efficiency, and reliability. With the ability to remove imperfections with remarkable accuracy, their advanced grinding techniques enhance product quality, reduce production time, and maximize cost-effectiveness.Innovation in CNC Machined Parts Grinding (approx. 200 words):Building on decades of experience and a commitment to continuous innovation, the company has introduced state-of-the-art advancements in CNC Machined Parts Grinding. By leveraging advanced robotic systems, high-precision tools, and computer numerical control (CNC) technology, they have transformed the grinding process, setting new standards in the industry.The integration of robotic systems has enabled precise handling and positioning of components, ensuring consistent grinding quality. This automation enhances productivity, eliminates human error, and optimizes production throughput. Additionally, it allows for multitasking capabilities, enabling simultaneous grinding of multiple parts, saving valuable time without compromising precision.Furthermore, the utilization of high-precision tools and cutting-edge abrasives guarantees the removal of imperfections with exceptional accuracy. By employing a combination of grinding wheels, belts, and discs designed for specific applications, the company ensures the highest level of precision, ensuring superior surface finishes and dimensional accuracy.To enhance the grinding process's efficiency, the company has incorporated CNC technology into their machining centers. This allows for seamless coordination between various machining operations, eliminating the need for multiple setups and tool changes. The result is faster cycle times, reduced downtime, and improved overall productivity.Benefits and Applications (approx. 250 words):The advancements in CNC Machined Parts Grinding have numerous benefits that make them indispensable for various manufacturing industries. The precision achieved through these techniques ensures the exact dimensions and tolerances required, eliminating the risk of errors and rework. By improving product quality and reducing rejects, manufacturers can establish a reputation for delivering superior components consistently.Moreover, these advancements have considerably reduced production time. With increased automation, multitasking capabilities, and efficient integration of CNC technology, companies can significantly improve throughput. This accelerates the delivery of finished parts, enabling manufacturers to meet tight deadlines without compromising quality.The cost-effectiveness of CNC Machined Parts Grinding is another crucial advantage. By streamlining processes and minimizing waste, manufacturers can optimize resource utilization and reduce production costs. In addition, the ability to complete complex grinding operations in a single setup reduces labor costs and machine downtime.The applications for CNC Machined Parts Grinding span various industries, including aerospace, automotive, robotics, medical, and more. In the aerospace sector, for instance, the precision grinding techniques are indispensable for creating intricate components that withstand the extreme demands of aircraft engines. Similarly, in the medical field, these advancements enable the production of high-precision parts for surgical instruments and prosthetics, ensuring utmost reliability and patient safety.Conclusion (approx. 70 words):Through their relentless pursuit of innovation, the company has transformed CNC Machined Parts Grinding, positioning themselves as industry leaders. With a focus on precision, efficiency, and cost-effectiveness, their advanced grinding techniques have revolutionized the manufacturing sector. By embracing these advancements, manufacturers can forge a path towards increased productivity, improved quality, and enhanced competitiveness in the global market.
Precision CNC Machined Parts for Corn and Grain Agriculture Products – Manufacturer in China
CNC machining is a widely-used technology in various industries, including agriculture. Specifically, CNC machined parts are essential in corn and grain harvesting and processing activities. In Senorok.com, we offer precision CNC machined parts that provide outstanding performance and optimal efficiency. Our expert manufacturing team uses the latest technology and an extensive range of raw materials to produce high-quality machined parts for different industries.One of our most popular CNC machined parts is the SS-03,05 model, which is made of high-quality steel. Steel is a durable and robust material that can withstand extreme conditions, making it ideal for use in agricultural machinery. With our precise CAD/CAM techniques and cutting-edge CNC technology, we can manufacture highly accurate and precise machined parts that meet our clients' unique demands.Our CNC machined parts are available at a reasonable price, and we offer competitive rates that make us a reliable partner for different types of businesses. Our team has years of experience in delivering top-quality CNC machined parts, and we understand the importance of delivering products that match our clients' expectations.Apart from steel, we can also manufacture CNC milled plastic parts that are highly effective in various applications. Plastic parts are preferred in some cases because they are lightweight, affordable, and can be quickly produced in large volumes. Our CNC machines are optimized to work with different types of plastics, and we can provide custom-made solutions that suit our clients' requirements.In conclusion, CNC machining is an essential technology that contributes significantly to the agricultural sector. At Senorok.com, we are committed to delivering top-quality CNC machined parts that provide superior performance and durability. Our products are reliable, competitively priced, and manufactured with precision to meet our clients' unique needs. Please contact us today to learn more about our CNC machining services and how we can help your business succeed.