What is Water-jet Technology? A Definition
By:Admin
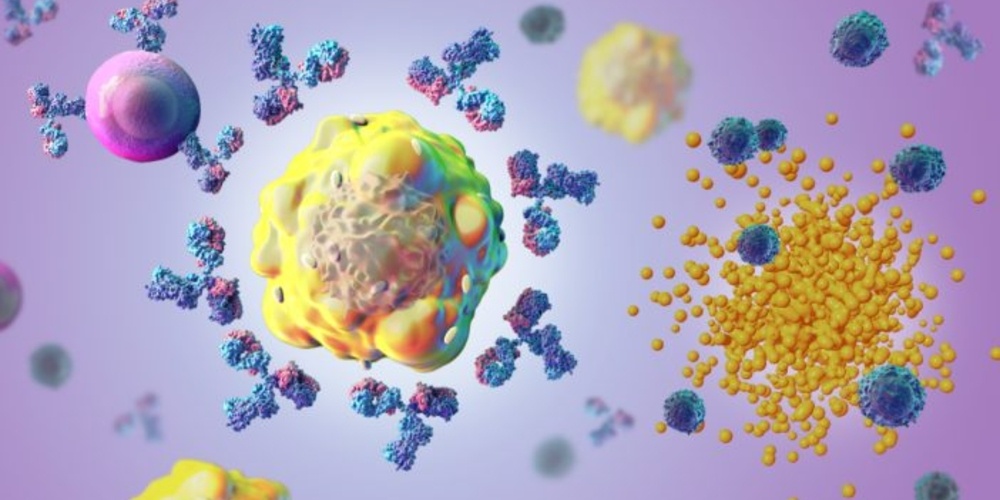
Water-jet technology has been quietly revolutionizing the industrial world over the past decade. Driven by powerful streams of water and sometimes abrasive materials, water-jet cutting technology is quickly becoming the go-to cutting method for a variety of industries. From aerospace to the medical field, water-jet cutting is proving to be more precise and efficient than traditional cutting methods.
A water-jet is a cutting tool that creates a high-velocity jet of water, usually mixed with an abrasive material. This creates a powerful cutting force that can cut through virtually any material with precision, including metal, stone, glass, and plastic. Water-jet cutting technology was developed in the 1950s, and since then, it has been continuously refined and improved, becoming one of the most versatile and effective cutting methods available today.
One of the many benefits of water-jet cutting is its precision. Unlike traditional cutting methods that rely on brute force and sharp blades, water-jet cutting relies on a powerful stream of water to slice through materials with ease. This allows for incredibly intricate and precise cuts, even on difficult or complicated materials.
Another benefit of water-jet cutting is its versatility. Water-jet cutters can handle a wide range of materials, from soft rubber to thick steel. This makes it an ideal choice for industries that require cutting precision on a variety of materials.
The aerospace industry, for example, heavily relies on water-jet technology for the precision cutting of parts and components. With water-jet cutting, aerospace manufacturers can create intricate shapes out of tough materials such as titanium and composites, resulting in stronger, lighter-weight aircraft that perform better than ever before. Other industries, such as the medical field, also rely on water-jet cutting for precision cutting of surgical instruments and implantable devices.
Water-jet cutting technology has also become more accessible in recent years, with more and more companies offering water-jet cutting services to a variety of industries. Companies like {} offer state-of-the-art water-jet cutting services that can handle large production runs or small, custom projects. By outsourcing their cutting needs, businesses can save time and money on equipment and maintenance costs while still enjoying the precision and versatility of water-jet cutting.
Finally, water-jet cutting is also environmentally friendly. Unlike traditional cutting methods that produce harmful dust and debris, water-jet cutting creates minimal waste and leaves the material clean and untouched. This means less waste, fewer environmental hazards, and a safer workplace for employees.
In conclusion, water-jet cutting technology is quickly becoming the go-to cutting method for businesses ranging from aerospace to medical manufacturing. With its precision, versatility, accessibility, and environmentally friendly benefits, water-jet cutting is the perfect solution for industries that require precise cutting of a variety of materials. As technology continues to improve, we can only expect to see water-jet cutting become even more essential to the industrial world.
Company News & Blog
Precision CNC Machining Services in Texas with Low Costs and Fast Lead Times
In the world of manufacturing, precision is paramount. The emergence of Computer Numerical Control (CNC) machines revolutionized the way manufacturers produced parts. CNC milling and turning are some of the most common machining processes, and with technological advancements, the processes have become more efficient, accurate, and cost-effective. 3D Hubs provides a CNC machining service in Texas that delivers low-cost, precision machined parts with an 8-day lead time from America, China, Europe, and India. CNC milling is a process that involves removing material from a workpiece using rotary cutters. The milling machine uses computer-aided design (CAD) to guide the cutting tool along different axes to achieve the desired shape. The machine can produce complex parts with a high level of precision and accuracy. The process is ideal for producing parts with intricate shapes, contours, and features that would be challenging to make using manual machining methods.CNC turning involves spinning a workpiece on a lathe machine while a cutting tool removes material to achieve the desired shape. The lathe machine uses CAD to guide the cutting tool along different axes. The process is ideal for producing round or cylindrical parts, including threads and grooves. Like CNC milling, the process is efficient and accurate, enabling the production of high-quality parts with tight tolerances.3D Hubs' CNC machining service in Texas utilizes both milling and turning processes to deliver high-precision, low-cost machined parts. The company uses computer-controlled machines that operate 24/7 to minimize lead times and reduce the cost of production. The machines are capable of machining a wide range of materials, including metals, plastics, and composites. The company's CNC milling machines use up to 5 axes, enabling the production of complex geometries with highly accurate finishes. The machines can produce parts with tolerances as tight as ± 0.005mm, ensuring that the parts meet the required specifications. The CNC turning machines, on the other hand, can produce parts with a diameter as small as 1mm and a length of up to 300mm. In addition to CNC milling and turning, 3D Hubs' CNC machining service in Texas includes finishing processes such as sandblasting, polishing, and anodizing. The finishing processes are essential to improve the appearance and functionality of the parts. Sandblasting, for instance, can give the parts a textured surface that improves their grip, while anodizing can enhance their corrosion resistance.3D Hubs' CNC machining service in Texas is ideal for businesses that require low-cost, high-precision machined parts. The company's ability to produce parts with tight tolerances, short lead times, and a wide range of materials makes it a valuable partner for manufacturers across different industries. The company's commitment to quality and customer satisfaction ensures that businesses get the best value for their money.In conclusion, CNC milling and turning are essential machining processes that have transformed the manufacturing industry. The processes are efficient, accurate, and cost-effective, making them ideal for producing high-quality parts with tight tolerances. 3D Hubs' CNC machining service in Texas utilizes these processes to deliver low-cost, high-precision machined parts with short lead times. With their commitment to quality and customer satisfaction, businesses can rely on 3D Hubs to provide the best value for their money.
MTConnect-Ready 3D Printer for Aerospace and Production Applications
, MTConnect, FDM, aerospace, production, 3D printing.Additive Manufacturing Magazine recently reported that the Stratasys Fortus 900 3D printer now features an MTConnect-ready interface. This is great news for those working in aerospace and other industries that require high-quality, production-grade 3D printing.The Stratasys Fortus 900 is a Fused Deposition Modeling (FDM) 3D printer designed for large, complex parts. With a build volume of 36 x 24 x 36 inches, it has the capability to produce parts that are larger than those typically produced with plastic extrusion machines. This makes it an ideal choice for aerospace applications, as well as for producing jigs, fixtures, and tooling.Incorporating the MTConnect protocol into the Stratasys Fortus 900 means that users can now monitor and control their 3D printing operations in real time. MTConnect is an open, royalty-free standard for machine tool communication that has become increasingly popular in the manufacturing industry. With MTConnect, users can easily connect machines and devices to a network, allowing them to monitor data and make informed decisions about their operations.For aerospace manufacturers, the Stratasys Fortus 900 with MTConnect-ready interface is ideal, as it provides the capability to produce production-grade parts with repeatable accuracy. Additionally, 3D printing allows for the production of complex geometries that cannot be produced with traditional manufacturing methods.Overall, the integration of MTConnect into the Stratasys Fortus 900 3D printer is a positive development for the additive manufacturing industry. By providing real-time monitoring and control, it enables users to optimize their operations, increase efficiency, and improve the quality of their products. This is especially important in industries such as aerospace, where high-quality, production-grade parts are essential.As the use of 3D printing continues to grow, we can expect to see further developments in this area, and the integration of other technologies into 3D printers. In the meantime, the Stratasys Fortus 900 with MTConnect-ready interface is a great option for those looking to produce high-quality, production-grade parts with 3D printing technology.
What is Water-jet Technology and How Does it Work?
Water-jet technology has evolved significantly over the years, providing a versatile and efficient solution for a range of industrial applications. This technology involves the use of a high-pressure pump to create a stream of water that can be used to cut, clean, and shape different materials. Water-jet technology is fast becoming the go-to option for many employers in varied industries.The process of water-jet cutting starts by using a high-pressure pump that pumps water through a nozzle, which produces a super-fast stream of water that is directed onto the material to be cut. The water pressure can be adjusted to suit the type of material being cut, from soft materials like plastic, rubber, and foam to hard materials like metals, ceramics, and glass.One of the most significant benefits of water-jet technology is its ability to perform intricate cuts without creating heat-affected zones (HAZ). Thermal distortion, discoloration, and other undesirable effects are often seen when traditional cutting methods are used, like plasm cutting. However, water-jet cutting ensures material integrity through cold cutting, making it ideal for precision machining, intricate architectural designs, medical equipment, aerospace, and automotive parts.Traditional cutting methods such as laser and plasma can produce toxic fumes or debris that can be dangerous to the environment and human health. In contrast, water-jet cutting is eco-friendly and safe. The water used in this process can be recycled and reused, and the cutting operation produces no hazardous waste, allowing companies to reduce their environmental footprint considerably.Moreover, water-jet technology requires no special tooling, which means changing between different materials and designs is a breeze. This makes water-jet cutting an even more attractive option for manufacturers who need to switch between various production requirements quickly. Additionally, with advancements in technology, 5-axis cutting technology and robotics can be utilized, allowing greater flexibility and increased accuracy in cutting, ensuring more efficient and cost-effective production.The benefits of water-jet technology are not limited to cutting and shaping applications, as it has other uses too. Water-jet cleaning is another application of this technology. It involves the use of high-pressure water streams to remove dirt and grime from surfaces, making it an effective cleaning option for many businesses. Cleaning using a water-jet is particularly useful in the food and beverage industry, where sanitation is critical.Another advantage of using water-jet technology in cleaning is that it does not require any chemicals to aid the cleaning process. This, in turn, ensures that the cleaned surfaces are safe for human consumption, eliminating the need for chemical-based cleaning agents harmful to the environment and humans. The use of water-jet technology in cleaning can significantly reduce washing times and increase production efficiency, making it an ideal solution for many businesses.In conclusion, water-jet technology presents an innovative and eco-friendly solution for many manufacturing and cleaning applications. Its benefits are unrivaled when compared to traditional cutting and cleaning technologies. From increased production efficiency to reduced environmental footprint to the ability to perform intricate and precise cuts, water-jet technology has fast become a sought-after option for many businesses looking to improve their bottom line. Companies that have not yet implemented this technology in their operations are urged to give it a try and discover the numerous cost and time-saving benefits it can offer.
Fast and Accurate CNC Turning Services for Precision Parts
Lathe machines are essential tools in the world of manufacturing. They are responsible for the creation of many of the intricate components that make up various products. Among the many types of lathes available, the CNC lathe stands out as one of the most advanced and precise. If you are in need of precision CNC lathe parts, then you need to partner with a reliable and experienced company, and latency is the perfect choice.At Lathe, we specialize in offering fast and accurate CNC turning services. Our lathe department is equipped with state-of-the-art CNC lathes and proven technology, positioning us to serve our customers' needs best. Our experienced and skilled machinists have the knowledge and training required to program even the most complex turning operations. As a result, we can produce highly precise parts while maintaining a fast turnaround time.Our lathes are equipped with cutting-edge technology that enables them to deliver exceptional accuracy, regardless of the complexity of the part. Additionally, our lathes have a range of spindle speeds, allowing us to handle a wide variety of materials, including aluminum, brass, copper, stainless steel, and more.We take quality seriously at Lathe, and we have put measures in place to ensure that our customers receive parts of the highest quality. First, we use state-of-the-art quality control equipment to verify that our parts meet the required specifications. Additionally, we have a team of experienced quality control technicians who conduct regular inspections to ensure that our parts meet our high-quality standards.We understand that time is of the essence in many manufacturing processes, which is why we are committed to offering fast turnaround times. Our efficient machining processes, combined with our team of skilled machinists, enable us to produce parts quickly and efficiently.In conclusion, if you are in need of precision CNC lathe parts, you need to partner with a reliable and experienced company. At Lathe, we have the equipment, technology, and skilled personnel required to deliver high-quality parts that meet your specifications. Contact us today to learn more about our CNC turning services and how we can help you with your manufacturing needs. And if you're searching for terms like "precision CNC lathe part", you can be sure that you've come to the right place.
Digitally Controlled Solutions for Precise Metal Bending in Steel, Stainless Steel, and Aluminum
: How Digitally Controlled Solutions Are Revolutionizing TFE Bending ServicesSheet metal bending has been an essential part of manufacturing since the industrial revolution, but advancements in digital control have allowed for greater levels of precision and efficiency. At TFE, these cutting-edge techniques are being applied to create bespoke sheet metal bending parts of the highest quality and accuracy.In 2018, TFE invested in new bending machines with digital control capabilities, allowing them to meet the increasing requirements of their clients. These machines provide the ability to bend a range of materials including steel, stainless steel, and aluminum, and the accuracy of the multi-station bending press allows for the creation of complex geometries with ease.The use of digital control allows TFE to achieve unparalleled precision, making it possible to create parts with crushed bends or plunging without the need for further reworking. This technology also ensures exceptional repeatability, allowing for a faster turnaround time on orders.The TFE bent metal parts portfolio is comprehensive, covering angular bending, variable radius bending, and crushed bends. However, TFE's capabilities don't stop there. They have also developed innovative methods for large radius stretching, an alternative to rolling or in addition to it. This approach provides unique opportunities for niche applications that require specific shapes of sheet metal parts.TFE takes great pride in their commitment to quality, and their innovative techniques guarantee a constant level of excellence. The company's digitally controlled bending methods allow for excellent man-machine complementarity, resulting in the highest levels of efficiency and productivity.In conclusion, TFE's bending services have been transformed with the integration of digitally controlled bending machines. These advanced techniques allow for the creation of bespoke parts with exceptional levels of accuracy, repeatability, and quality. If you're in the market for sheet metal bending parts, look no further than TFE for the most innovative and precise solutions. Keywords: TFE Bending, Sheet Metal Bending Parts, Digital Control, Bending Machines, Multi-Station Bending Press, Repeatability, Angular Bending, Variable Radius Bending, Crushed Bends, Large Radius Stretching, Man-Machine Complementarity, Precision, Efficiency, Productivity.
What is Water-jet Technology? A Definition
Water-jet Technology Takes the Industrial World by StormWater-jet technology has been quietly revolutionizing the industrial world over the past decade. Driven by powerful streams of water and sometimes abrasive materials, water-jet cutting technology is quickly becoming the go-to cutting method for a variety of industries. From aerospace to the medical field, water-jet cutting is proving to be more precise and efficient than traditional cutting methods.A water-jet is a cutting tool that creates a high-velocity jet of water, usually mixed with an abrasive material. This creates a powerful cutting force that can cut through virtually any material with precision, including metal, stone, glass, and plastic. Water-jet cutting technology was developed in the 1950s, and since then, it has been continuously refined and improved, becoming one of the most versatile and effective cutting methods available today.One of the many benefits of water-jet cutting is its precision. Unlike traditional cutting methods that rely on brute force and sharp blades, water-jet cutting relies on a powerful stream of water to slice through materials with ease. This allows for incredibly intricate and precise cuts, even on difficult or complicated materials.Another benefit of water-jet cutting is its versatility. Water-jet cutters can handle a wide range of materials, from soft rubber to thick steel. This makes it an ideal choice for industries that require cutting precision on a variety of materials.The aerospace industry, for example, heavily relies on water-jet technology for the precision cutting of parts and components. With water-jet cutting, aerospace manufacturers can create intricate shapes out of tough materials such as titanium and composites, resulting in stronger, lighter-weight aircraft that perform better than ever before. Other industries, such as the medical field, also rely on water-jet cutting for precision cutting of surgical instruments and implantable devices.Water-jet cutting technology has also become more accessible in recent years, with more and more companies offering water-jet cutting services to a variety of industries. Companies like {} offer state-of-the-art water-jet cutting services that can handle large production runs or small, custom projects. By outsourcing their cutting needs, businesses can save time and money on equipment and maintenance costs while still enjoying the precision and versatility of water-jet cutting.Finally, water-jet cutting is also environmentally friendly. Unlike traditional cutting methods that produce harmful dust and debris, water-jet cutting creates minimal waste and leaves the material clean and untouched. This means less waste, fewer environmental hazards, and a safer workplace for employees.In conclusion, water-jet cutting technology is quickly becoming the go-to cutting method for businesses ranging from aerospace to medical manufacturing. With its precision, versatility, accessibility, and environmentally friendly benefits, water-jet cutting is the perfect solution for industries that require precise cutting of a variety of materials. As technology continues to improve, we can only expect to see water-jet cutting become even more essential to the industrial world.
How to Build a Heavy CNC Milling Machine: 18 Steps with Pictures
Machine, Instructables, heavy CNC milling, epoxy granite, linear guides, building processCNC Milling Machine: A Comprehensive Guide to Building Your OwnBuilding a heavy-duty CNC milling machine is not a task for the faint-hearted. It requires a lot of different working steps and careful planning to ensure that you end up with a machine that can deliver precise and accurate results. In this blog post, we will take a closer look at the steps involved in building a big CNC machine with good milling performance, as well as the materials and equipment needed for the project.Step 1: Design and PlanningThe first step in building a CNC milling machine is to design and plan the machine. This involves deciding on the size of the machine, the materials to be used, the type of milling machine to be used, and the features and capabilities that the machine should have. It is important to have a clear understanding of the requirements before starting the project to avoid any costly mistakes down the line.Step 2: Building the MoldThe next step is to build a big and accurate mold for casting the epoxy granite. Epoxy granite is a popular material for building milling machines due to its sturdiness and vibration damping properties. The mold should be designed to ensure that it is rigid and can create a smooth surface finish. The casting process should be done carefully to avoid any air bubbles or voids that can cause inaccuracies in the finished cast.Step 3: Aligning the Linear GuidesThe linear guides play a crucial role in the accuracy and precision of the milling machine. They are responsible for guiding the cutting tool along a straight and consistent path. The linear guides should be aligned carefully to ensure that they are in perfect alignment with the cutting tool. This requires careful attention to detail and the use of precision measuring tools.Step 4: Building the Machine FrameThe frame of the milling machine should be built to be strong and rigid. The use of high-quality materials such as aluminum or steel is recommended. The frame should be designed with sufficient clearance to accommodate the linear guides and other machine components.Step 5: Assembling the MachineOnce all the components of the milling machine have been prepared, it is time to start assembling the machine. This requires careful attention to detail and a lot of patience. Each component should be installed carefully and securely to ensure that the machine is stable and can deliver precise and accurate results.ConclusionBuilding a heavy CNC milling machine is a challenging task that requires a lot of time and effort. However, with careful planning and attention to detail, it is possible to build a machine that can deliver precise and accurate results. The use of high-quality materials and precision measuring tools is essential to ensure that the machine is built to the required specifications. With the right approach, anyone can build their own CNC milling machine and take their machining capabilities to the next level.
Sheet Metal: A Fundamental Form in Metalworking
Title: Sheet Metal Flat: Revolutionizing Industrial Fabrication ProcessesIntroduction:(sheet metal flat logo)Sheet Metal Flat is a renowned leader in the field of sheet metal fabrication. With a commitment to innovation and quality, the company continues to revolutionize the manufacturing industry. Their expertise lies in the production of thin, flat pieces of metal that can be easily cut and shaped into various forms. This article delves into the significance of sheet metal fabrication, explores the various applications, and highlights Sheet Metal Flat's contributions to this field.Importance of Sheet Metal Fabrication:Sheet metal fabrication plays a pivotal role in numerous industries, making it one of the fundamental forms used in metalworking. By utilizing industrial processes, sheet metal is transformed into thin, flat pieces which can then be molded into a variety of shapes. This versatility enables the creation of countless everyday objects that are an integral part of our lives.Applications of Sheet Metal:The applications of sheet metal fabrication are vast and diverse. From the automotive sector to construction, aerospace, and even household appliances, sheet metal is an essential component in the production of various products. It is widely used in the manufacturing of automobile parts, including body panels, chassis, and engine components due to its durability, strength, and resistance to corrosion.In the construction industry, sheet metal is utilized for roofing, facades, and structural elements due to its lightweight nature and high durability. The aerospace industry leverages sheet metal for aircraft structures, providing strength, stability, and resilience at high altitudes. In household appliances, sheet metal is employed in the manufacturing of refrigerators, stoves, and washing machines due to its ability to withstand high temperatures and repeated use.Sheet Metal Flat: Pioneers in Fabrication:Sheet Metal Flat has emerged as a reliable and innovative player in the sheet metal fabrication industry. The company's commitment to cutting-edge technology and exceptional quality has positioned them as a distinguished leader.Efficient Manufacturing Processes: Sheet Metal Flat employs state-of-the-art machinery and equipment to ensure precision and efficiency in their manufacturing processes. From laser cutting to stamping, bending, and welding, they have perfected every stage of fabrication. This enables them to deliver superior end products while ensuring timely production.Custom Solutions: Recognizing the unique requirements of each client, Sheet Metal Flat offers customized solutions tailored to suit their specific needs. Their team of experienced technicians works closely with customers, providing expert guidance and utilizing cutting-edge software to design and create flawless sheet metal components.Quality Assurance: Sheet Metal Flat is committed to delivering products of the highest quality. Rigorous quality control measures, including inspections at different stages of production, are in place to ensure that every piece meets the highest standards. By adhering to strict quality control protocols, Sheet Metal Flat has fostered long-lasting relationships with their clients.Environmental Responsibility: In an era of increasing environmental awareness, Sheet Metal Flat is committed to minimizing their carbon footprint. They have implemented eco-friendly practices such as recycling scrap metal, reducing waste generation, and incorporating energy-efficient machinery. By choosing Sheet Metal Flat, customers can align with their sustainability goals.Conclusion:Sheet Metal Flat's contribution to the sheet metal fabrication industry cannot be understated. With their innovative manufacturing processes, commitment to quality, and dedication to customer satisfaction, they have set new benchmarks in the field. As the demand for sheet metal continues to grow across various sectors, Sheet Metal Flat is poised to remain at the forefront, constantly pushing the boundaries of possibility and redefining the standards for industrial metalworking.
China-Based Manufacturer Offers Precision CNC Machined Parts
Wintec Precision Machining Co., Ltd: Your One-Stop Solution for CNC Precision Machined ComponentsWintec Precision Machining Co., Ltd is a leading OEM/ODM manufacturer of CNC precision machined components in China. With years of experience in the industry, Wintec has emerged as a reliable and trustworthy machining partner for businesses across the globe. Our team of highly skilled engineers and technicians, along with state-of-the-art infrastructure and advanced technology, enable us to deliver high-quality machined products that are second to none.At Wintec, we operate with a customer-first approach where customer satisfaction is our top priority. We work closely with our clients to understand their specific requirements and offer customized solutions that meet their needs. We have an extensive range of machining capabilities, including CNC turning, CNC milling, and CNC grinding, to provide accurate and precise parts that meet our client's specifications.Our CNC precision machined components are made using strict quality control measures that ensure superior product performance and reliability. We use only the highest quality raw materials that are sourced from reputable suppliers to ensure that our products meet stringent industry standards. Our commitment to quality is demonstrated by our ISO 9001:2015 certification, a testament that we deliver quality products consistently.At Wintec, we offer a broad range of CNC precision machined components, including shafts, sleeves, gears, housings, and more. We specialize in producing quality parts that cater to a wide range of industries, including the automotive, aerospace, medical, and energy sectors. Our machining capabilities allow us to create parts with intricate designs, intricate surface finishes, and tight tolerances that meet our client's exacting requirements.As a China-based manufacturer, Wintec offers our clients a cost-effective solution that does not compromise on quality. We have an extensive network of suppliers that allows us to source the best raw materials at a competitive price, passing on the savings to our clients. Our commitment to delivering cost-effective solutions makes us an attractive partner for businesses looking to reduce their production costs without sacrificing quality.In conclusion, Wintec Precision Machining Co., Ltd is a reliable partner for businesses in need of CNC precision machined components. We offer quality products, customized solutions, and cost-effective services that meet our clients' requirements. Our commitment to customer satisfaction, quality, and integrity makes us the ideal choice for your machining needs. Contact us today to learn more about our products and services.
High Precision Vacuum Casting Filament for Consistent Layering and Easy Support Removal
and 3D printing.In today's fast-paced technological world, 3D printing has become increasingly popular, revolutionizing the way we design and create products. One of the key features of 3D printing is the new range of materials available which can produce high-quality and accurate printed products. Vaccum Casting is one such material that is perfect for the production of complex or intricate parts.Vaccum Casting is a thermoplastic elastomer that is commonly used in 3D printing. Its unique properties make it a perfect choice for printing objects that require precision and accuracy. With an extrusion temperature ranging from 175-200C, Vaccum Casting is an ideal option for printing small and delicate parts. The filament also has high roundness and precision of +/- 0.01 mm, ensuring that your print is accurate and of high quality.One of the key benefits of Vaccum Casting is that it sticks nicely to glass/kapton tape heated bed, resulting in no first-layer problem. This makes it easier to work with as it ensures that the print stays in place while printing. Additionally, the filament extrudes precisely for fast printing and consistent layering, which results in better prints overall.Filament comes in a light/compact spool, in a sealed package with a bag of desiccant, which ensures that the filament remains dry and of high quality. The desiccant is a moisture-absorbing material, which means that even if the filament is kept in a humid environment, it will not absorb the moisture and will be of high quality during printing.Another key benefit of Vaccum Casting is that it is easy to remove support material. When printing complex or intricate parts, support material is often required to ensure that the parts maintain their shape and structure. Vaccum Casting's easy-to-remove support material feature ensures that you can quickly and easily remove the material and finish your prints.In conclusion, Vaccum Casting is an excellent material for 3D printing, with its unique properties making it ideal for producing small and complex parts. Its high roundness and precision make it ideal for printing objects that require accuracy and precision. The ease of removing support material and the ability to stick nicely to a heated bed are other benefits that make Vaccum Casting a preferred option for 3D printing. So, if you're looking for a reliable and precise filament for 3D printing, be sure to try Vaccum Casting.